A circuit board is a combination of different types of layers that contribute to its functionality, making it the right choice for a variety of tasks. Regardless of the type of board, each PCB consists of layers of different materials that provide support during assembly and operations. Sometimes, circuit boards need to be kept safe before implementing in the device and during operation too. Applying certain finishes and coatings are not alone sufficient but keeping the surface clean is of utmost importance.
What is the importance of having a clean PCB surface?
Cleaning a printed circuit board is as important as manufacturing it. If not cleaned properly, it can lead to damaged connections, loose components, and can affect the soldering process and material properties as well. Hence, it is advisable to take the same care in selecting the right cleaning method as taken when designing, specifying, and producing the board in the first place.
Board contaminants could be dry and wet. Dirt and dust are dry contaminants and grime, oil, and flux fall under wet contaminants. Compressed air, ultrasonic cleaning, and vacuum cleaning are some sought-after choices for PCB cleaning but need due attention.
The most reliable PCB assembly in Silicon Valley
Avoid component procurement delays by using a single vendor to source your parts. Transparent pricing. Fast turn-times.
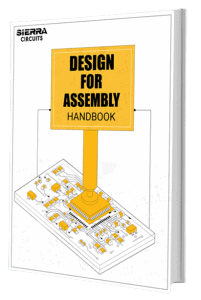
Design for Assembly Handbook
6 Chapters - 50 Pages - 70 Minute ReadWhat's Inside:
- Recommended layout for components
- Common PCB assembly defects
- Factors that impact the cost of the PCB assembly, including:
- Component packages
- Board assembly volumes
Download Now
Types of surface layers that support board assembly process
Surface finish
Circuit boards have a base copper surface that is prone to oxidation if left without a protective coating, which is why the surface finish is needed. It is also used for preparing the board surface for soldering components onto the board during assembly and for enhancing the board’s shelf-life. Some of the most popular PCB surface finishes are HASL, ENIG, and ENEPIG (used for military and space applications).
Solder mask layer
The solder mask layer, also called solder resist or solder stop mask, is applied on the top of the unpopulated PCB. Having green color in general, it covers all copper features on the board surface and insulates them from oxidation. The primary objective is to prevent accidental solder bridging between neighboring pads and traces during assembly. Note that the solder mask layer is completely different from the conformal coating as the latter is applied to protect the assembled board.
Importance of solder mask layer
- Prevents accidental solder bridging during assembly, hence reduces the amount of rework required for removing shorts
- Averts solder starvation when molten solder flows down the track, resulting in an inadequate amount of solder in the pad
- Prevents oxidation of copper traces and features
Nowadays, fabricators prefer to use liquid photo imageable solder masks as it offers ease of use, higher durability, and reliability.
How to check if the solder mask file is correct?
The best way to check is to look at the top copper layer and top mask layer at the same time. They should be aligned so you can see exactly where mask clearances will be in relation to the copper. Follow the same technique for the bottom layer.
By default, the entire board is covered with a solder mask, on both the top and bottom sides. Always mention this in the fabrication drawing if you need it or not. Additionally, Gerber output should contain a separate mask file for the top and bottom layers.
Via covering
Via covering is a way of completely or partially covering the PCB vias since open vias can cause undesired conductive paths due to accumulated solder paste. It is usually a solder mask or any other non-conductive material that protects the via from solder paste, dust, or any other particles. There are two types of via coverings available: tented and non-tented.
Importance of via covering
The presence of an uncovered via near a pad lets molten solder paste wick into its hole, making the pad starve for adequate solder. Covering the via with a solder mask prevents this.
Silkscreen
PCB assembly is a comprehensive process of soldering components onto the board surface. It is not only about placing components casually but also following the rules specific to electrical requirements, polarity markings, and circuit board design needs.
Silkscreen layer is applied mainly to specify human-readable markings such as:
- Component reference designators
- Polarity marking
- Pin 1 marking
- Component boundaries
- Company logos
- Manufacturer marks
- Warning symbols
- Part numbers
- Version numbers
- Date code
Silkscreen printing can be done by manual screen printing, liquid photo imaging (LPI), and direct legend printing (DLP).
One-stop PCB assembly services, capabilities, and testing
We source components from chip manufacturers across the globe, including Mouser, Digi-Key, Arrow Electronics and others. We also warehouse a significant inventory of common parts. If we cannot source a specific component, our engineers will make recommendations for fair-price alternatives. Get started now.