Contents
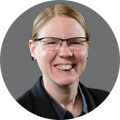
On-demand webinar
How Good is My Shield? An Introduction to Transfer Impedance and Shielding Effectiveness
by Karen Burnham
The surface-mount IC packages assembled on a PCB are available in different types. The most popular ones are the QFN packages.
These miniature packages are suitable for consumer electronics, automotive designs, and industrial and power applications.
There is much to learn regarding their types, features, design, and assembly.
What does QFN stand for?
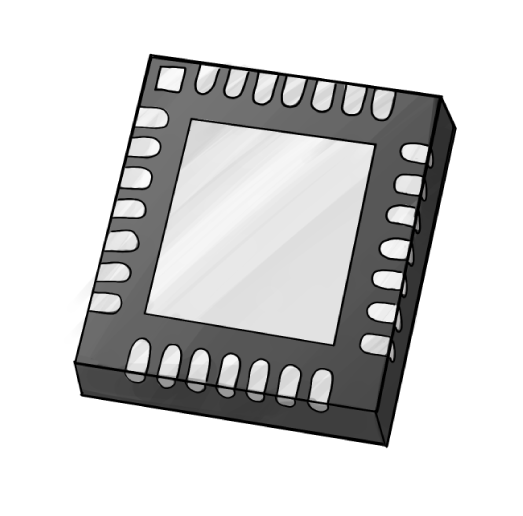
QFN is an acronym for quad flat no-lead package. It is a leadless package that comes in small size and offers moderate heat dissipation in PCBs. Like any other IC package, the function of a QFN package is to connect the silicon die of the IC to the circuit board.
What’s inside a QFN package?
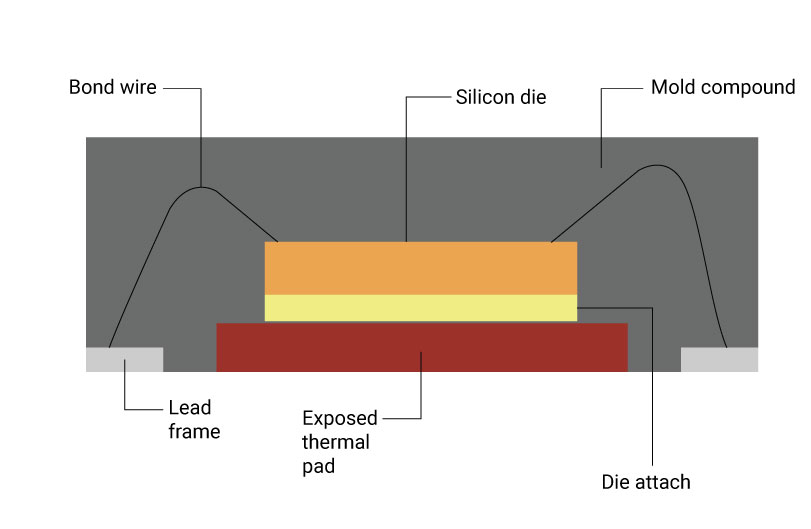
The QFN packages come with a die surrounded by a lead frame. The lead frame is made up of a copper alloy with a matt tin coating.
The die and the frame are usually connected to each other using wire bonding. Copper/gold is usually preferred for wire bonding. Some manufacturers use flip-chip technology for this interconnection. The flip-chip technique offers better electrical performance compared to the conventional one.
The metalized terminal pads are located at the bottom surface. These terminal pads are present along the four edges of the bottom surface and provide electrical interconnections to the PCB.
The bottom side of the package consists of an exposed pad. This pad provides an efficient heat path to the PCB. The exposed pad enables ground connection as well.
The QFN package is soldered to the circuit board at the exposed pad. The die attach is the epoxy material used to fix the die to the exposed pad.
For thermal management in PCBs, check out 12 PCB Thermal Management Techniques to Reduce PCB Heating.
The following are some of the properties of standard QFN packages:
- 0.35mm to 2.10mm maximum seated height (standard: 0.85 mm)
- Terminal platings of Ni-Pd-Au and Sn
- Halogen-free and lead-free
- RoHS, ELV, and REACH compliance
The commonly used variants of QFN packages include thin QFN (TQFN), very-thin QFN (VQFN), micro lead-frame (MLF), etc.
Advantages of QFN packages
- Quad flat no-lead packages come in lightweight and are easy to handle.
- These packages are available in a thin profile and a small form factor.
- The bond wires used to connect the die and frame are short.
- The lead inductance of these packages is low.
- They are ideal for applications that require good heat dissipation.
- These packages are easily available at a low cost.
What are the different types of QFN packages?
Based on the method of molding, the QFN packages are classified into punch-type and sawn-type packages.
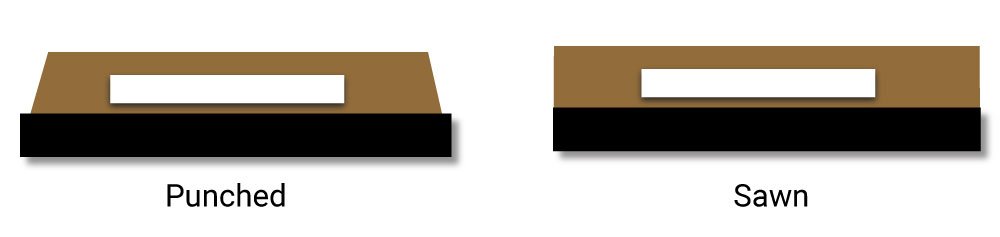
Punch-type
In punch-type singulation, the package is molded in the single mold cavity format and is separated using a punch tool. This means that only a single package is molded into shape using this method.
Sawn-type
These packages are molded using the mold array process (MAP). This method involves cutting a large set of packages into parts.
A final saw process helps to separate the sawn-type packages into individual packages.
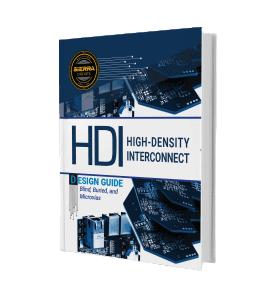
HDI PCB Design Guide
5 Chapters - 52 Pages - 60 Minute ReadWhat's Inside:
- Planning your stack-up and microvia structure
- Choosing the right materials
- Signal integrity and controlled impedance in HDI
- Manufacturing considerations for higher yields
Download Now
What are the different QFN package terminal pads?
The terminal pads of the QFN can be different from each other on the basis of their design, shape, and dimensions. Given below are the different types of terminal pads available.
Fully exposed terminal ends
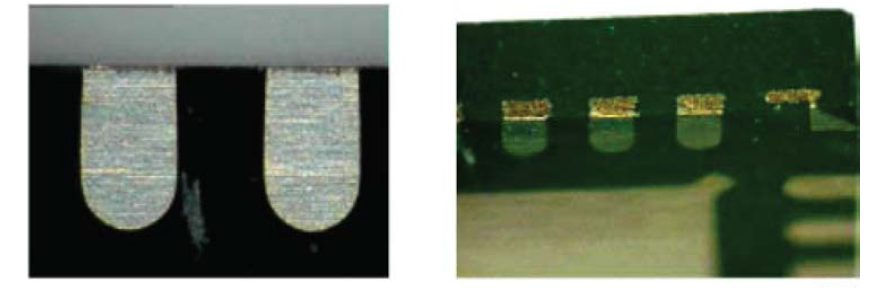
In this type, the terminal ends are fully exposed all the way to the edge of the package and to the side of the package.
Pull-back terminal ends
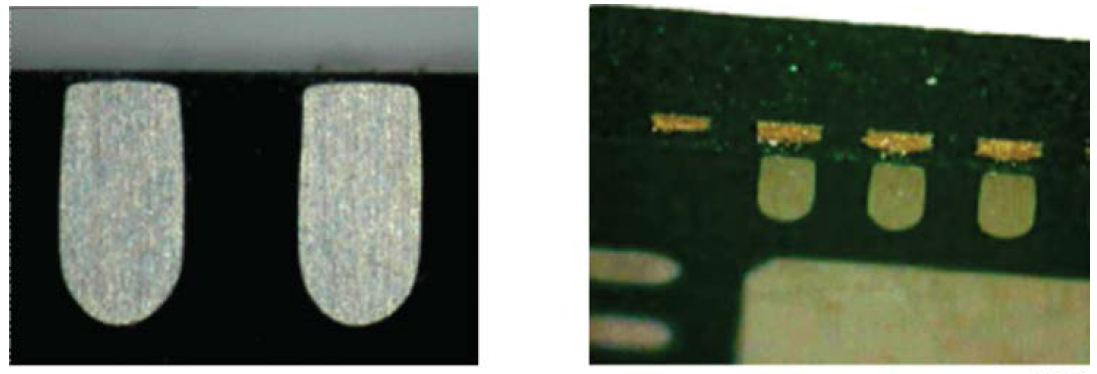
The terminal ends are pulled back from the edges of the package. Solder fillets are not added after the reflow soldering process for this type of terminal end packages.
Side wettable flank terminal ends
These types of terminal ends are an altered form of fully exposed terminal ends. Side wettable flank terminal ends enable solder wetting for the formation of solder fillets. The solder failure inspection using AOI becomes easier if uniform solder fillets are formed. This eliminates the need for X-ray inspection.
QFN footprint design
While designing the footprint for the QFN refer to the datasheet of the component. The datasheet will have the package outline drawing. This drawing forms the basis for the footprint design.
The detailed package outline of an HVQFN48 package from NXP is given below:
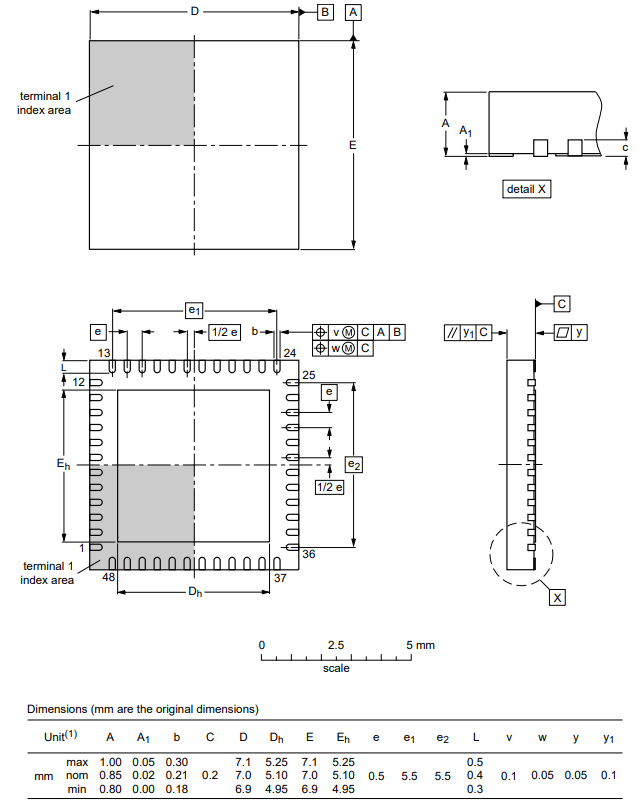
The following things must be taken care of while designing the footprint of a QFN package:
- Orientation marking/pin 1 marking.
- The ground pad (EP pad) should have a sufficient number of vias for heat dissipation.
- Check the solder mask and solder paste layers. Keep the openings as recommended by the manufacturer.
- Solder web should be 4mil or more.
The figure below shows the recommended footprint for the same HVQFN48 package:
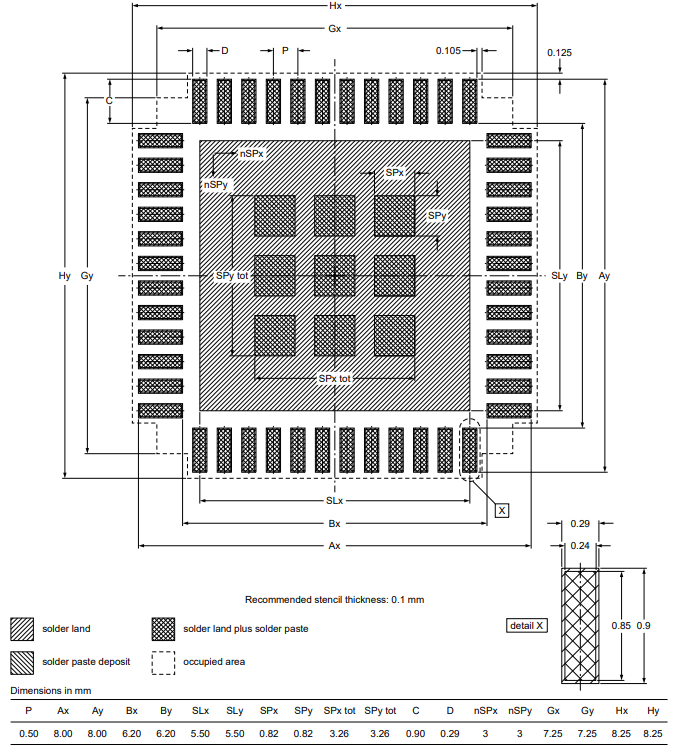
QFN assembly
The following are the basic steps involved in the surface-mount assembly of the QFN components:
- Solder-paste printing: Solder paste printing is the process of uniformly spreading the solder paste on the board before placement of components.
- Component placement: The QFN IC components are mounted on the circuit board as per the layout decided during the PCB design stage. Since these components have high interconnection density, precise and accurate pick and place tools are used.
- Pre-reflow inspection: Pre-reflow inspection is done to ensure that the board is ready to go into the reflow oven. This helps to remove contaminants on the surface of the board that may interfere with the soldering process.
- Reflow soldering: QFN components are commonly soldered using reflow soldering.
- Post reflow inspection: This inspection is done to check the quality of the soldering.
A proper PCB footprint and stencil design are required for the assembled components to operate as per the design intent.
Also read, Thermal profile for solder reflow.
How are QFN packages soldered on a PCB?
Soldering is a part of the QFN assembly process. During the assembly process, the components are mounted after solder paste screening. After QFN components are mounted using a pick and place tool, they are soldered using reflow soldering. When the PCB goes into a reflow oven, the temperature inside will make certain areas of the board heat faster than the rest. The heavier components and large copper areas will take more time to get heated.
The top surface temperature of the QFN package is monitored using thermocouples throughout the process. This is to check that the peak package body temperature (TP) does not exceed the standard values.
How are the QFN solder joints inspected?
The solder joints of the QFN components are formed underneath the package. Hence for the inspection of these, optical inspection and X-ray inspection are used.
Rework on assembled components
If a defect is noticed post-assembly on any QFN component, that particular component can be removed and replaced. Special rework stations are available for this purpose. A rework station should have the following components.
- Split-light system: acts as a vision system to observe the bottom side of the package and the site on the PCB.
- An X-Y table for alignment.
- A hot-air system with top and bottom heaters for component removal.
The procedure for rework is given below.
- A pre-bake process is done before heating to avoid any moisture-related failures of the board and the components.
- The next step is de-soldering, and the temperature profile of the board and the components should be kept in mind.
- Once de-soldering is done, the component should be mechanically removed. For large components, pipettes can be used and for smaller ones, tweezers are a good option.
- After removal, the PCB pads should be cleaned to remove any solder residue. This also prepares the site for the new component placement.
- The placement of the new component takes place through the same steps mentioned earlier during assembly.
What is the difference between QFN and QFP?
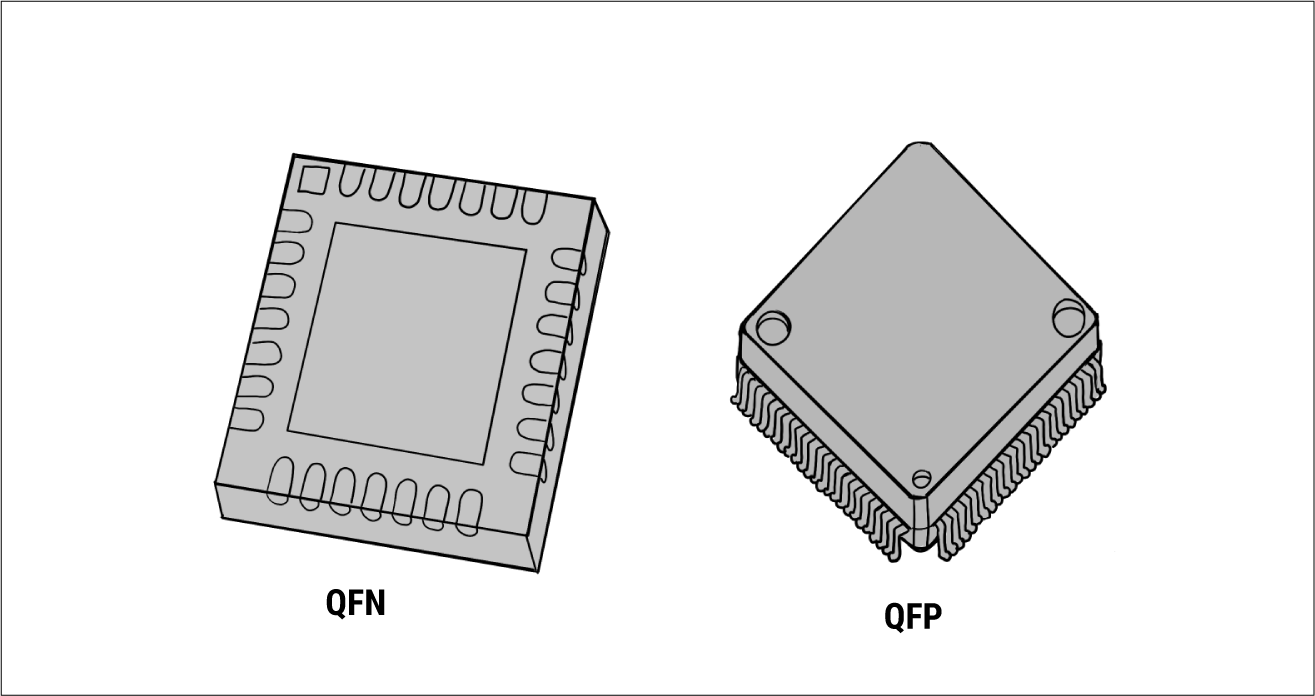
A Quad flat package (QFP) is also a surface mount integrated circuit package. In QFP, unlike QFN, the leads extend out in a gull-wing shape (L-shaped). This provides a good footing for the package during the PCB assembly process.
Just like QFN, the leads extend out on all four sides of the package, hence the name quad flat package.
QFP packages with different numbers of pins are available, starting from 8 pins per side to 70 pins per side. QFP32, QFP64, etc. are some examples. The usual pin spacing ranges from 0.4mm to 1mm.
Variants of the QFP package include thin QFP (TQFP), very thin QFP (VQFP), low-profile QFP (LQFP), etc.
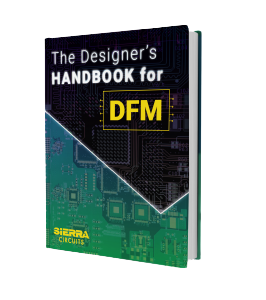
Design for Manufacturing Handbook
10 Chapters - 40 Pages - 45 Minute ReadWhat's Inside:
- Annular rings: avoid drill breakouts
- Vias: optimize your design
- Trace width and space: follow the best practices
- Solder mask and silkscreen: get the must-knows
Download Now
What is LQFP64 package?
LQFP64 is an example of a low-profile QFP with 64 pins and offers the same advantages as QFP. The difference is that LQFP comes with a thinner body thickness (1.4mm). They have a standard lead-frame footprint of 2mm.
Because of their small size and heat-dissipating characteristics, QFN IC packages are widely used. The available QFN variants are suitable for a broad range of applications. Hence QFN packages are in high demand when it comes to surface-mount packages.
Let us know if you have any queries about QFN on our forum, SierraConnect. Our experts will answer them.
Start the discussion at sierraconnect.protoexpress.com