Contents
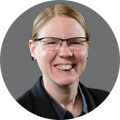
On-demand webinar
How Good is My Shield? An Introduction to Transfer Impedance and Shielding Effectiveness
by Karen Burnham
IPC-2221 establishes standards for PCB design aspects such as schematic, material selection, thermal management, DFM, DFA, DFT, and quality assurance. Some of the primary design requirements of high-voltage boards are defined in IPC-2221B.
They include conductor spacing, creepage, and insulation requirements. Before diving into the details, let’s have a look at IPC standards in general.
What are IPC standards?
IPC standards are established for the electronic manufacturing industry and are issued by a trade association named IPC. It lays the foundation for the design, assembly, packaging, interconnection, material, performance, and inspection specifications for the electronic industry. These global standards are pivotal to achieving high-yield circuit boards. Adhering to these standards can reduce the communication between the designer and the manufacturer.
Importance of the IPC-2221 standard
IPC-2221 sheds light on the prerequisites for designing organic circuit boards with effective component placement, and interconnection structures. These boards are built using organic PCB materials or a combination of organic and inorganic substrates.
This benchmark incorporates high-voltage electrical considerations such as PDN bus layouts, conductor spacing, heat dissipation, controlled impedance, and test coupon design.
Features:
- The results are based on IPC 2221B standard, table 6-1 (table.1 and 2 in this article)
- Supports all the conductor configurations as defined in the standard
- Computes the minimum spacing between two conductors
- Calculates maximum voltage between the copper features for a known clearance
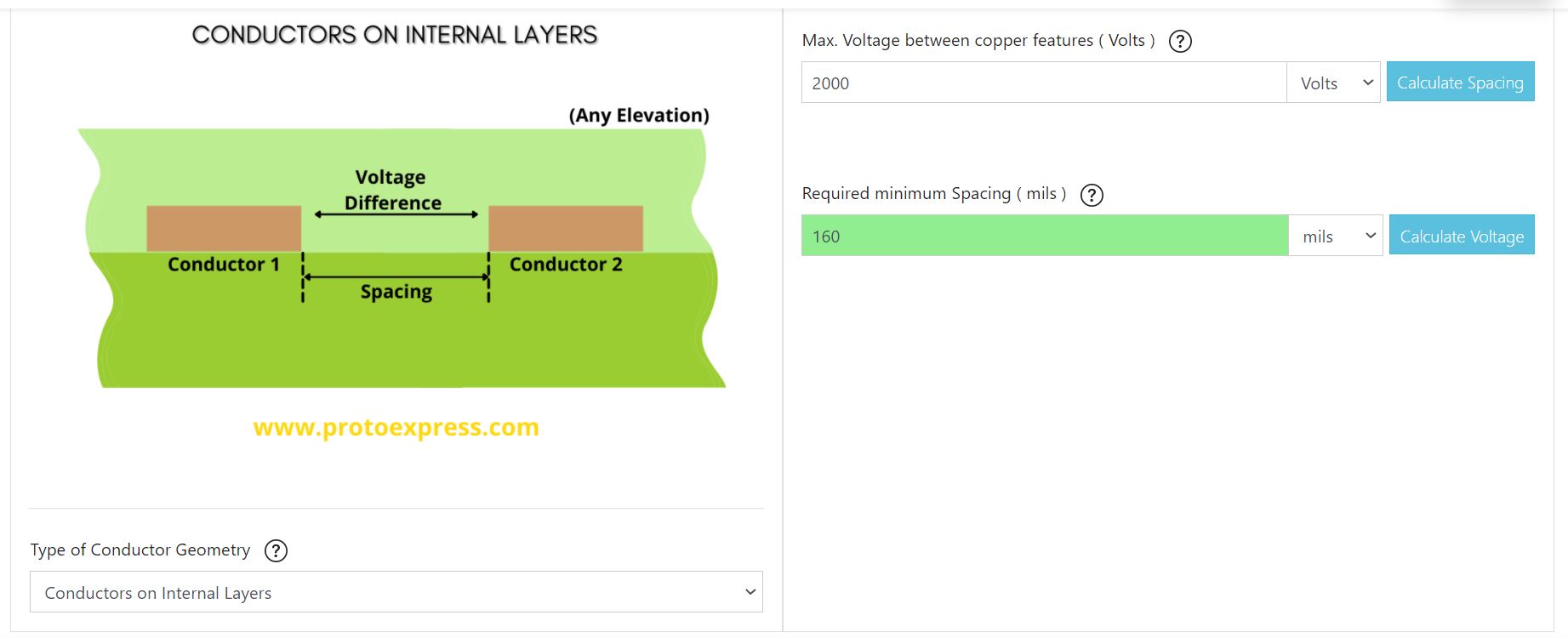
Hierarchy of IPC-2221 documentation
IPC-2221 is the bedrock of the IPC-2220-FAM design series, based on which the design principles and recommendations for different kinds of boards are established. The hierarchy of the 2220 series is shown below.
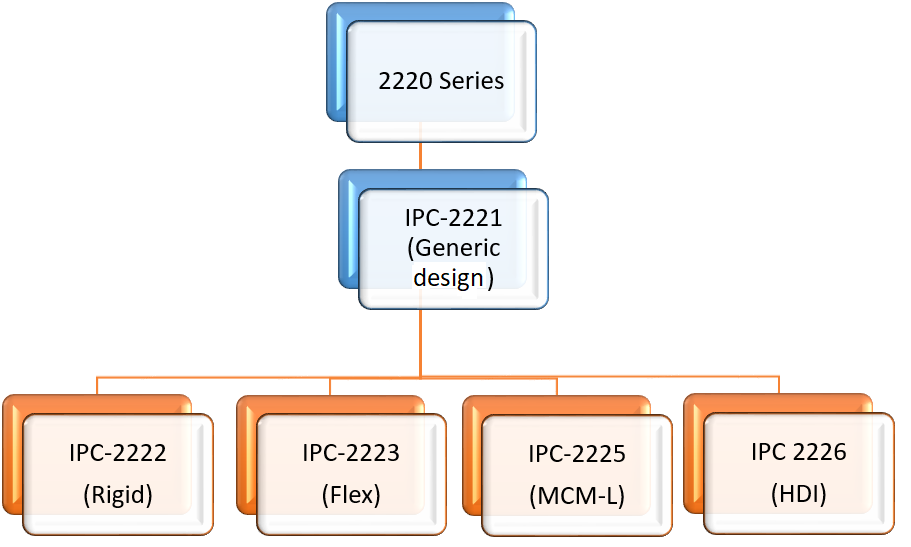
You need to consider the generic standards established by IPC-2221 in conjunction with the detailed requirements specific to your design. For example, to design a rigid board, the regulations mentioned in IPC-2221 should be referred to alongside the ones laid out in IPC-2222.
IPC-2222: sectional standard for rigid boards
IPC-2222 mentions the optimized rules for efficient component placement, routing density, and superior electrical performance to achieve a flawless design. Used in conjunction with IPC-2221, IPC-2222 sets standards for the following factors to increase the manufacturability of a rigid circuit:
- Holes and interconnections specifics
- Dielectric spacing
- Selection of materials
- Routing parameters
- Board thickness tolerance
- Mechanical parameters
IPC-2223: sectional standard for flex circuits
The key design considerations, mentioned in IPC-2223, for designing a perfect flex board, are listed below:
- Material selection and construction
- Selective plating
- Minimum bend radius for flexible circuits
- How to achieve controlled impedance
- Unsupported edge conductor design
- Filling of via
- Pad placement
IPC-2224: standards for designing PWBs with PC Cards
The IPC-2224 standard is a set of requirements for designing PC cards. The standard also guides you to secure passive and active components such as through-hole, fine-pitch BGAs, unpackaged bare die, array mount, and surface mount devices. The material specifications ensure faultless physical, thermal, and electrical functions of the following types of boards:
- Type I: Single-sided circuit board
- Type II: Double-sided circuit board
- Type III: Multilayer board without blind or buried Vias
- Type IV: Multilayer board with blind or buried Vias
- Type V: Multilayer metal core board without blind or buried Vias
- Type VI: Multilayer board with metal core and blind or buried vias
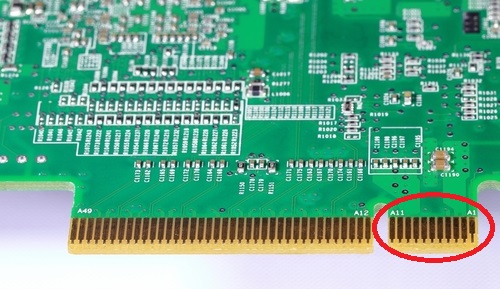
IPC-2225: designing organic multichip modules (MCM-L) and MCM-L assemblies
IPC-2225 establishes the regulations for designing and assembling bare chips on the substrate. This incorporates adhesive details, attached dies, and microvia materials.
IPC-2226: standards for designing HDI boards
IPC-2226 establishes design considerations for HDI structures. The standard provides attributes for power, ground, signal, and combined layer details, information on dielectric separation, via formation, and other crucial factors of the HDI substrate.
It classifies HDI boards into six industry-accepted categories. The classification is based on the number and location of the circuit layers that may or may not connect to the substrate. The [C] symbol is used if the layers are adjacent to the core. For passive connections, [P] is implemented. For instance, an HDI board with two layers on one side of the core and one layer on the opposite layer can be represented as 2 [C] 1. Following are the definitions applicable to HDI circuits:
- Type I (1 [C] 0 and 1 [C] 1): Through vias connecting the outer layers.
- Type II (1 [C] 0 or 1 [C] 1): Buried vias in the core and may have through vias connecting the outer layers.
- Type III ( ≥ 2 [C] ≥ 0 ): The core may have buried vias or through vias connecting the outer layers.
- Type IV (≥ 1 [P] ≥ 0): Here P is a passive substrate with no electrical connection.
- Type V: Constructions without a core.
- Type VI: Other constructions.
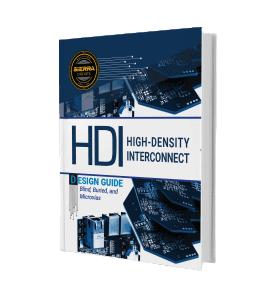
HDI PCB Design Guide
5 Chapters - 52 Pages - 60 Minute ReadWhat's Inside:
- Planning your stack-up and microvia structure
- Choosing the right materials
- Signal integrity and controlled impedance in HDI
- Manufacturing considerations for higher yields
Download Now
Significance of IPC-2221 in high-voltage design
IPC-2221B mostly addresses two major issues:
- Risk of dielectric breakdown in a strong high-electric field: It can be eliminated by choosing the right material, spacing, and insulation, and also by maintaining cleanliness.
- Possibility of anodic filamentation
The minimum spacing details required to allow high voltage between two conductors are specified in the standard. These values are evaluated with respect to peak DC or AC voltage. A point to be observed is that IPC-2221 mentions the exact minimum spacing required to pass voltage at around 500 V. If the voltage exceeds 500V, per-volt clearance calculation will help you obtain the necessary minimum spacing.
Table. 1 Minimum clearance values for a bare board to pass voltages of a specific range
Voltage between conductors (Volts) | Minimum clearance for bare board | |||
---|---|---|---|---|
Internal conductors | External conductors, uncoated, up to sea level 3050 m | External conductors, uncoated, over sea level 3050 m | External conductors, with permanent polymer coating (any elevation) | |
0-15 | 0.05 mm | 0.1 mm | 0.1 mm | 0.05 mm |
16-30 | 0.05 mm | 0.1 mm | 0.1 mm | 0.05 mm |
31-50 | 0.1 mm | 0.6 mm | 0.6 mm | 0.13 mm |
51-100 | 0.1 mm | 0.6 mm | 1.5 mm | 0.13 mm |
101-150 | 0.2 mm | 0.6 mm | 3.2 mm | 0.4 mm |
151-170 | 0.2 mm | 1.25 mm | 6.4 mm | 0.4 mm |
171-250 | 0.2 mm | 1.25 mm | 6.4 mm | 0.4 mm |
251-300 | 0.2 mm | 1.25 mm | 12.5 mm | 0.4 mm |
301-500 | 0.25 mm | 2.5 mm | 12.5 mm | 0.8 mm |
Greater than 500 | 0.025 mm/volt | 0.005 mm/volt | 0.025 mm/volt | 0.00305 mm/volt |
Table. 2 Minimum clearance values for an assembled board to pass voltages of a specific range
Voltage between conductors (Volts) | Minimum clearance for assembled board | ||
---|---|---|---|
External conductors, with a conformal coating over assembly (any elevation) | External conductors lead/termination, uncoated, up to sea level 3050 m | External conductors lead/termination, with a conformal coating (any elevation) | |
0-15 | 0.13 mm | 0.13 mm | 0.13 mm |
16-30 | 0.13 mm | 0.25 mm | 0.13 mm |
31-50 | 0.13 mm | 0.4 mm | 0.13 mm |
51-100 | 0.13 mm | 0.5 mm | 0.13 mm |
101-150 | 0.4 mm | 0.8 mm | 0.4 mm |
151-170 | 0.4 mm | 0.8 mm | 0.4 mm |
171-250 | 0.4 mm | 0.8 mm | 0.4 mm |
251-300 | 0.4 mm | 0.8 mm | 0.8 mm |
301-500 | 0.8 mm | 1.5 mm | 0.8 mm |
Greater than 500 | 0.00305 mm/volt | 0.00305 mm/volt | 0.00305 mm/volt |
Table credit: IPC-2221
IPC-2221 standards for clearance and creepage
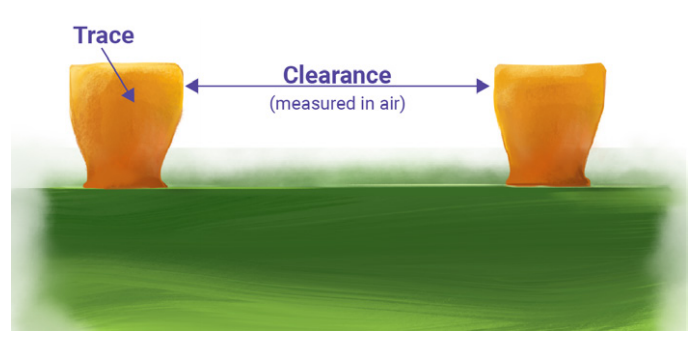
Clearance and creepage are two parameters that are related to the distance required between conductors on a circuit board. The distance between two conductors or nodes, measured in air, is referred to as the clearance distance. IPC-2221 defines optimum clearances related to different aspects of the circuit board. Let us have a look at a few of the important ones mentioned in this standard.
Table. 3 Optimum clearance required for specific features
Feature | Clearance |
---|---|
Component leads | 0.13 mm (up to a voltage of 50V) |
Uncoated conducting areas (washers or similar mechanical hardware) | 0.75 mm |
Test probe sites | 80% of the component height (0.6 mm minimum and 5 mm maximum) |
Mounting hardware | Should not protrude more than 6.4 mm below PCB surface |
PTH relief in the heat sink | 2.5 mm larger than the hole (includes electrical clearance and misregistration tolerance) |
Table. 4 IPC-2221 mask clearance and dams values for solder masks
Mask type | Clearance | Dam |
---|---|---|
Liquid screenable | 0.25 mm | 0.25 mm |
Photoimageable dry film ≤0.0635mm | 0.051 mm | 0.127 mm |
Photoimageable dry film 0.066 to 0.1mm | 0.051 mm | 0.25 mm |
LPI | 0.051 mm | 0.1 mm |
To learn about prevalent solder mask errors and techniques to avoid them, see 6 common solder mask errors every PCB designer should know.
Creepage, on the other hand, refers to the distance between conductors or nodes along the surface of an insulator.
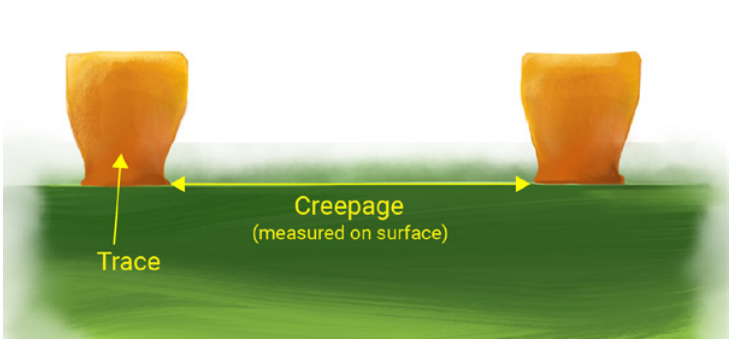
As per IPC-2221, space between the conductors should always be maximized to the possible extent. Conductor spacing needs to be optimized in such a manner that there is enough space for the etch compensation of the other physical features. This etch compensation should be twice the etched copper thickness. Apart from the etch compensation, it should also consider conductor imperfections and copper wicking between PTHs and adjacent plane layers.
How thick should PCB traces be?
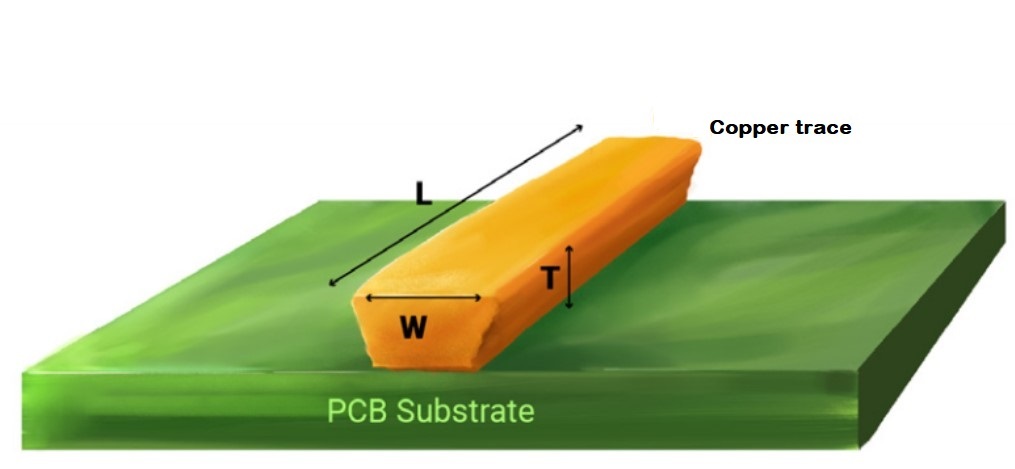
For carrying a specific amount of current, a PCB trace should have an appropriate thickness. If it is less than the required, the trace will burn while the current propagates through it. Thus, the thickness and width of the traces will depend on the signal characteristics, the current carrying capacity, and the maximum allowable temperature.
This is determined by referring to IPC-2141 and IPC-4562 as well. The thickness of the traces will also change according to the constructional requirements of the board. If the circuit board stack-up involves sequential lamination, and blind or buried vias, then deciding on the thickness of copper on the layers becomes crucial.
To calculate the trace width for allowable current, the following formula can be used:
Width [mil]=Area [mil2] / (Thickness [oz] x 1.378 [mil/oz])
The cross-sectional area, A is calculated by:
A = ( I / [k x (ΔT0.44)](1/0.725)
Where I is the maximum current in Amps, k is a constant, ΔT is the temperature rise above ambient in °C, and A is the cross-sectional area of trace in mil².
For internal layers,
- k = 0.024
- Conductor thickness = copper foil thickness of the base laminate.
- If blind and buried vias are implemented, then, the conductor thickness includes the copper plating thickness as well.
For external layers,
- k = 0.048
- Conductor thickness = thickness of the base foil and the plated copper of PTH without including the thickness of the solder coating, tin-lead plating, or secondary platings.
IPC-2221 insulation resistance test recommendations
Insulation is a basic requirement in a PCB for protection against short circuits, overheating, and corrosion. A lot of materials can be used to insulate a circuit board. The choice of the material, however, depends on the board’s application
IPC-2221 suggests some insulation resistance tests and individual test coupons as follows.
Insulation tests
- Insulation resistance test: In this test, a voltage is applied across the circuit board, which induces current flow. This current is measured to calculate the quantifiable resistance value for the entire product’s insulation.
- HiPot testing: This kind of test is used to check whether the insulation provided is enough to protect the circuit board or not. For this test, a high voltage is applied to the board and the resulting current flow through the insulation is measured. This current is called the leakage current, and it is measured using the HiPot tester. If the high voltage does not break down the insulation, then the insulation will be good enough to protect the board. This test is also known as the dielectric withstanding voltage (DWV) test and is usually carried out after the dielectric breakdown test.
Insulation resistance test coupons
- Moisture and insulation resistance coupons: These test coupons help to evaluate the insulation resistance and the bulk resistance of the circuit board. Here, the board is inspected by exposing it to different humidity and temperature environments with specific voltages applied to it.
- E-coupon: The moisture and insulation resistance of the laminated base materials are verified using this coupon. A design with a maximum of 10 layers can be tested using an E-coupon.
- Legacy E coupon: This coupon with a Y pattern aids in evaluating the cleanliness and insulation resistance properties.
Surface insulation resistance coupons
The surface insulation resistance test coupons include the following:
- H coupon: This involves measuring the effects of the process or residues on the surface insulation resistance.
- Legacy H coupon: Higher-level insulation testing requires using the legacy H coupon, such as for PCBs used in telecommunications.
To learn the ways to manage black pads in ENIG surface finish see, how to work around black pad in ENIG finish.
Standards for high-voltage circuits
The clearances mentioned in IPC-2221 require rechecking when it comes to high-voltage circuit boards. This is because there are more chances of a flashover in high-voltage designs than in a standard one. Therefore, different regulations should be considered in the case of high-voltage PCBs.
Selection of insulation materials
The materials used for insulation play a prominent role in withstanding the high potential between two conducting features. The best way to guarantee good insulation in high-voltage circuits is by choosing materials with comparative tracking index (CTI) ratings that can withstand high voltages. CTI is the measure of the electrical insulation of a material by subjecting it to a high voltage and monitoring the voltage at which it breaks down.
Increasing the clearance and creepage
With the increase in voltages, it is obvious that the clearance and creepage distance between traces and conducting features on the PCB should be increased. But we are working on circuit boards here, and hence there is a limit to which these distances can be increased. The minimum creepage and clearances defined by the IPC-2221 will not be enough to prevent a flashover in this case. Therefore, different methods should be adapted to increase the clearance and creepage distances for a high-voltage design. They include:
- Create slots, v-grooves, or parallel-sided notches between the conducting features
- Incorporate SMT components in abundance on the board, the ones that require maximum clearance from each other can be placed on opposite sides of the board
- Install vertical insulator barriers in the space
- Place high-voltage circuits on the top side of the board and low-voltage ones on the bottom to mitigate the chances of flash-over or arcing
IPC-2221 is a reference document that lays down a number of design standards while designing a PCB. Adhering to these standards is crucial to realize DFM, DFA, and DFT specs. Let us know in the comments section if you require any assistance to make your board manufacturable in the first go. Our design and manufacturing experts will be happy to help you.
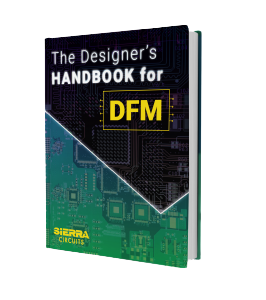
Design for Manufacturing Handbook
10 Chapters - 40 Pages - 45 Minute ReadWhat's Inside:
- Annular rings: avoid drill breakouts
- Vias: optimize your design
- Trace width and space: follow the best practices
- Solder mask and silkscreen: get the must-knows
Download Now