Contents
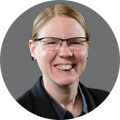
On-demand webinar
How Good is My Shield? An Introduction to Transfer Impedance and Shielding Effectiveness
by Karen Burnham
Annular rings are one of the biggest concerns for PCB designers. Even a slight misalignment during manufacturing can result in tangencies or breakouts, impacting the reliability of your printed board.
Highlights:
- Annular establishes a reliable connection between a via and the copper trace.
- Use teardrop pads to increase the structural integrity of narrow traces (<20 mil).
- Ensure the ring width meets or exceeds the manufacturer’s minimum requirements to prevent tangency or breakouts.
In this article, you’ll learn the importance of annular rings, and how to calculate accurate ring size to avoid common issues such as tangency and breakout.
What is an annular ring?
An annular ring is the area of the copper pad around a drilled and finished hole. The finished hole we are discussing here is a copper-plated via. All around this via there should be enough copper to form a solid connection between the copper traces and the via in a multi-layer PCB.
Therefore, the main purpose of an annular ring is to establish a good connection between a via and the copper trace.
The annular ring provides an area for connecting leads or wires to the electronic component, which serves as an anchor for the circuit.
Construction of an annular ring
When connecting traces to another layer in a multi-layered board, you typically have to place a copper pad on your circuit board and drill a via on it to make the connection. The outer ring surrounding the via after the PCB drilling process constitutes the annular ring.
To learn how to design a cost-efficient PCB without board respins, download our eBook.
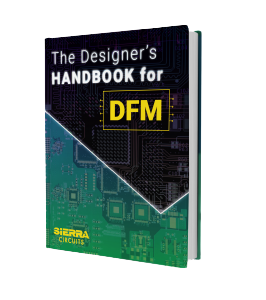
Design for Manufacturing Handbook
10 Chapters - 40 Pages - 45 Minute ReadWhat's Inside:
- Annular rings: avoid drill breakouts
- Vias: optimize your design
- Trace width and space: follow the best practices
- Solder mask and silkscreen: get the must-knows
Download Now
How do you calculate the annular size?
Ideally, designers want their annular rings with holes located dead-center to get the best connection possible between the vias and the layers.
The perfect width is the difference between the diameter of the copper pad and the diameter of the finished hole divided by two.
Annular ring size = (diameter of the pad – diameter of the finished hole) / 2
For example, if your pad diameter equals 22 mil and the hole diameter equals 10 mil, then the annular ring size is calculated in this manner: (22 – 10) / 2 = 6 mil.
Why does the ring size matter?
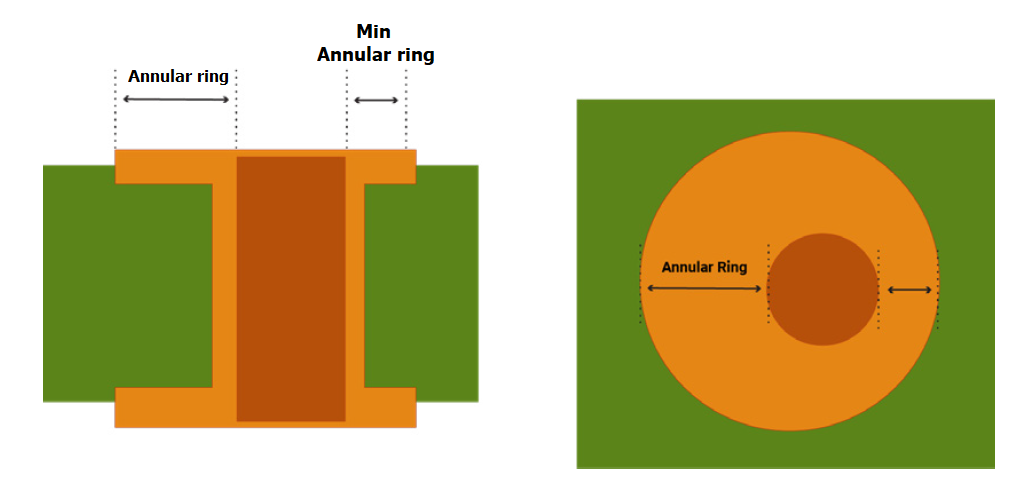
The annular ring should be sufficiently wide to ensure a reliable electrical connection with the via. The minimum width of the ring should be greater than or equal to the specified width for the design.
If the ring width is less than specified in the design, it can hinder component attachment and lead to pad breakout (zero annular ring), where the circuit overlaps or exits the pad. This reduces the circuit’s current-carrying capacity and compromises reliability.
Common annular ring issues
- Undesired annular ring
- Tangency
- Breakout
All of the above may arise due to insufficient ring width in the design.
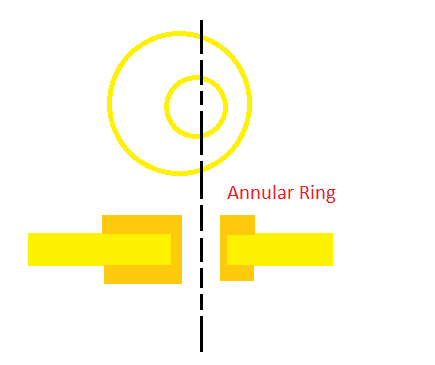
Download our design guide to learn about design for assembly.
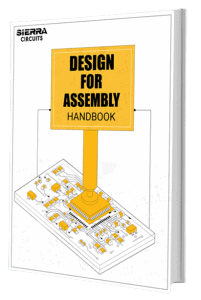
Design for Assembly Handbook
6 Chapters - 50 Pages - 70 Minute ReadWhat's Inside:
- Recommended layout for components
- Common PCB assembly defects
- Factors that impact the cost of the PCB assembly, including:
- Component packages
- Board assembly volumes
Download Now
How does the annular ring width affect the breakout probability?
The via hole must be drilled at the absolute center of the pad to form the annular ring or the minimum width of the ring must be above the specified value. Misregistration of the via concerning the land can lead to marginal interconnections that exhibit increased resistance and perhaps lead to reliability problems.
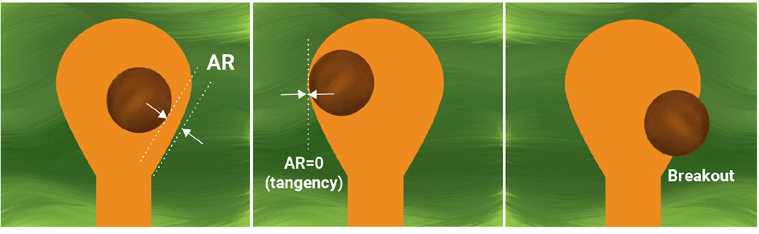
The graph below displays the probability of breakout plotted vs the annular ring.
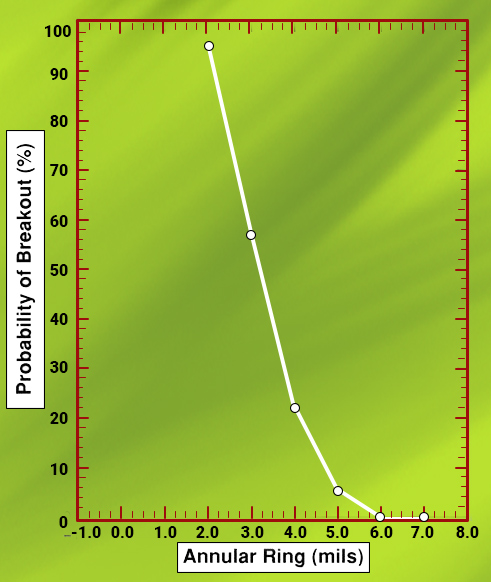
The smallest clearance (-1 mil) is intentionally designed to fail as a test to verify that the correct hole size was drilled. The probability of breakout decreases significantly, starting at 98% for a 2 mil clearance and dropping to 0% for clearances of 6 or 7 mil.
If the breakout is not acceptable, the supplier in this example would need to fabricate designs with annular rings of 6 mil or larger for the microvias. For 5 mil annular rings, the data indicates that 5% of the microvias will experience a breakout.
What is a teardrop pad?
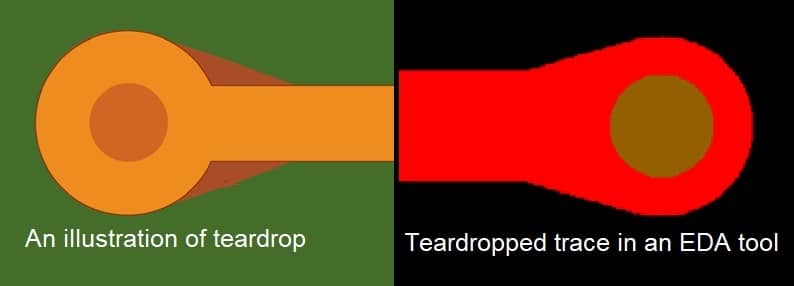
The name teardrop is used because of its shape. A teardrop pad is an extra feature that adds additional copper at the junction of annular rings with PCB traces. This shape can increase the structural integrity against mechanical or thermal stress.
During the drilling process, there is a possibility of misalignment of the drill bit which removes too much copper from the junctions of a via pad and PCB trace causing the possibility for a broken trace connection or too thin of a connection.
In such cases, a teardrop shape can increase the manufacturer’s tolerance of drill in the pad which can help reduce the rejection count in the production.
The importance of using teardrop increases as the traces become narrow. Teardrop rings are not necessary for conductors bigger than 20 mil. Also, teardrops are recommended for flex PCBs because of their structural integrity against shear and vibration.
An annular ring plays a critical role in PCB design and manufacturing. Hence, it’s a good practice to make sure all your annular rings are carefully crafted.
How Sierra Circuits can help you
Designing for manufacturing is the key to success. The free Better DFM is an online tool that checks your design for manufacturability. When using this tool, you can go to “Advanced Options “and choose what you need to check for in your annular rings. You now have several options:
- Tangency is the default option. If you are willing to accept tangency on pads in your manufactured board, the Better DFM will look for a minimum of 5 mil (0.005″) annular ring width in your design.
- When you need to have a minimum 1 mil ring on pads in your manufactured board, then the Better DFM will look for a minimum of 6 mil (0.006″) annular width in your design.
- If you are targeting a ring of a minimum 2 mil on pads in your manufactured board, the tool will look for a minimum of 7 mil (0.007″) ring width in your design.
- Lastly, if you do not mind having breakouts on pads in the manufactured board, the Better DFM will practically not look for any minimum ring width in your design. However, this option is not recommended.
The Better DFM does not only check for annular rings. The tool does a comprehensive design for manufacturability (DFM) analysis on your files.
The Better DFM tool’s 41-point checklist includes the following DFM checks:
Category | Checklist items |
---|---|
Signal checks | 1. Conductor width 2. Spacing 3. Annular ring 4. Drill to copper 5. Hole registration 6. Text features 7. Missing copper 8. Features connection 9. Missing holes 10. Unconnected lines 11. Route to copper |
Plane checks | 12. Drill to copper 13. Annular ring 14. Spacing 15. Conductor width 16. Thermal air gap / spoke width 17. Missing copper 18. Route to copper 19. Drill registration 20. Clearance smaller than the hole |
Solder mask checks | 21. Solder mask clearance 22. Coverage 23. Route to mask 24. Spacing 25. Missing solder mask clearance 26. Exposed lines 27. Partial clearances |
Silkscreen checks | 28. Silkscreen to mask spacing 29. Line width 30. Silkscreen to copper spacing 31. Silkscreen to hole spacing 32. Text height 33. Silkscreen to route spacing 34. Silkscreen over copper text |
Drill checks | 35. Hole size 36. Duplicate holes 37. Hole spacing 38. Touching holes 39. Plane shorts 40. Holes to route 41. Missing holes |
Key takeaways:
- Ensure the copper pad around the drilled hole (via) is sufficient to establish a solid connection between copper traces and vias in multi-layer PCBs.
- Use the formula:
Annular ring width = (Diameter of the pad – Diameter of the finished hole) / 2 to calculate the annular ring width accurately. - Ensure the via hole is drilled in the center of the pad to prevent the copper from touching the edge of the pad.
- Design annular rings wide enough to avoid pad breakouts, which can reduce circuit reliability.
- Incorporate tolerances in your design to account for potential mechanical or thermal stress during manufacturing and operation.
Need assistance in designing your annular rings Post your queries on our PCB forum, SierraConnect, and have them answered by our experts.
Start the discussion at sierraconnect.protoexpress.com