Contents
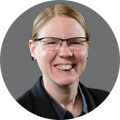
On-demand webinar
How Good is My Shield? An Introduction to Transfer Impedance and Shielding Effectiveness
by Karen Burnham
Drilling is the most expensive and time-consuming process in board manufacturing. The PCB drilling process must be carefully implemented since even a small error can lead to a great loss. The drilling process is considered the most critical bottleneck of printed circuit board manufacturing. A PCB design engineer must always look into the board manufacturer’s capabilities before placing an order.
The drilling process is the foundation for vias and the connectivity between different layers. The downsizing of electronic devices such as TVs and phones has led to their transformation from stationary to portable. High-quality micromachining is required to reduce the size. Drilling plays a vital role in making this possible. Hence, the implemented drill technology matters.
The PCB Drill Tech
Basically, there are two kinds of drilling technologies: mechanical and laser drilling.
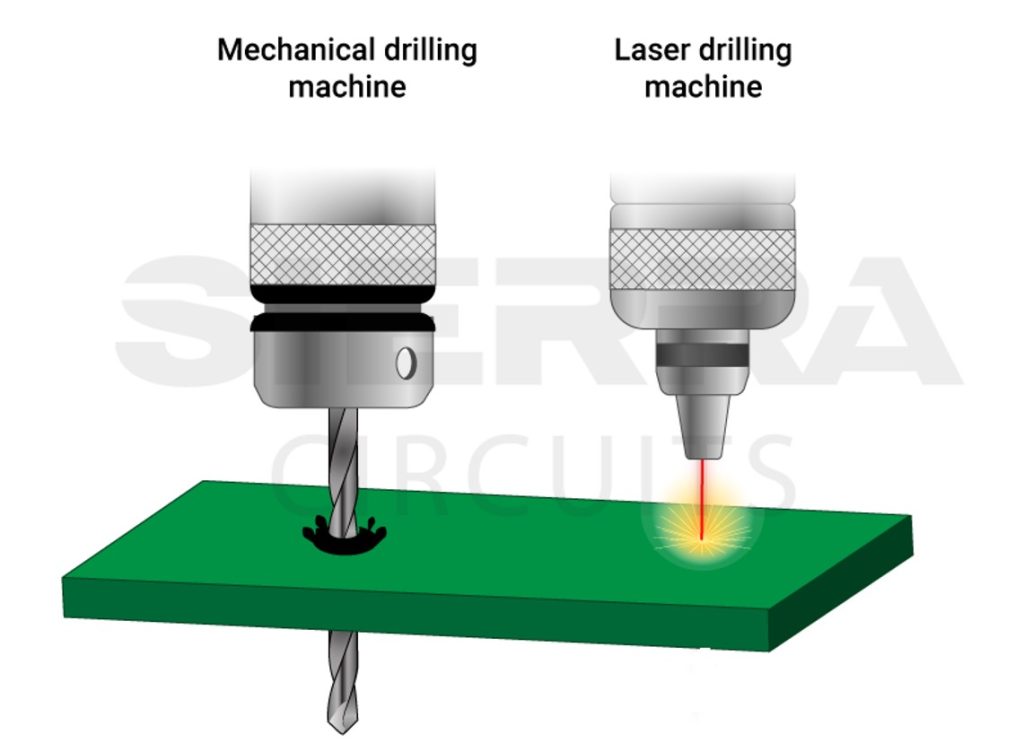
Mechanical drilling
Mechanical drills are less precise but easy to execute. This drilling technology uses drill bits. The smallest hole diameter that can be drilled by these drills is about 6 mil (0.006”).
Mechanical drill limitations
When used on softer materials like FR4, the mechanical drills can deliver 800 hits. For denser materials like Rogers, the lifespan is reduced to 200 counts.
If a PCB manufacturer ignores this, faulty holes will result, turning the board into scrap. The superior Hitachi drilling machines are implemented at Sierra circuits with a 1 mil hole placement tolerance.
Laser drilling
Laser drills, on the other hand, can drill much smaller holes. Laser drilling is a non-contact process in which the workpiece and the tool do not come in contact. A laser beam is used to remove board material and create precise holes. Here, the drill depth can be effortlessly controlled.
The laser technology is used to drill controlled depth vias with ease. Here, a minimum hole diameter of 2 mils (0.002”) can be drilled with precision.
Laser drilling limitations
A circuit board is made of copper, glass fiber, and resin. These PCB materials have different optical properties, making it difficult for the laser beam to burn through a board efficiently.
The cost of the process is also comparatively high in the case of laser drilling.
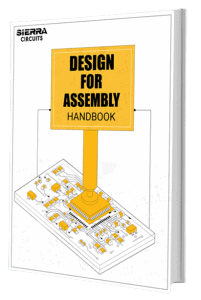
Design for Assembly Handbook
6 Chapters - 50 Pages - 70 Minute ReadWhat's Inside:
- Recommended layout for components
- Common PCB assembly defects
- Factors that impact the cost of the PCB assembly, including:
- Component packages
- Board assembly volumes
Download Now
It is better if the designer understands what happens on the shop floor to get a better perception of how the design is brought to life.
With this insight, the board designer ensures that the designs are manufacturable. This, in turn, reduces the cost, and the product can be delivered in a minimum turnaround time.
What happens on the shop floor?

After the lamination process, the laminated board is loaded on a panel of exit material on the drill bed. The exit material lessens the burr formation. Burr is the protruding part of copper formed when the drill spindle penetrates through the board.
On top of this panel, more stack-ups are loaded and are carefully aligned. In the end, a sheet of aluminum foil is placed over this entire stack-up. The Aluminium foil avoids entry burr and also dissipates the heat generated by the rapidly spinning drill bit.
Once the required number of holes are drilled, the boards are sent for the deburring and desmearing process.
Tool geometries must be considered since the quality of the drilled hole is crucial. High-speed steel (HSS) and tungsten carbide (WC) are commonly used drill bit materials for drilling composites.
Carbide tools offer better tool life during the machining of glass fiber-reinforced polymer (GFRP). The cemented carbide drills are generally used in PCB drilling.
Point angle and helix angle
The PCB drills have a point angle of 130° with a helix angle from 30° to 35°. A point angle is situated at the top of the drill bit. It is measured between the most prominent cutting edges.
A helix angle is an angle between the flanks of a drill bit at their intersection points.
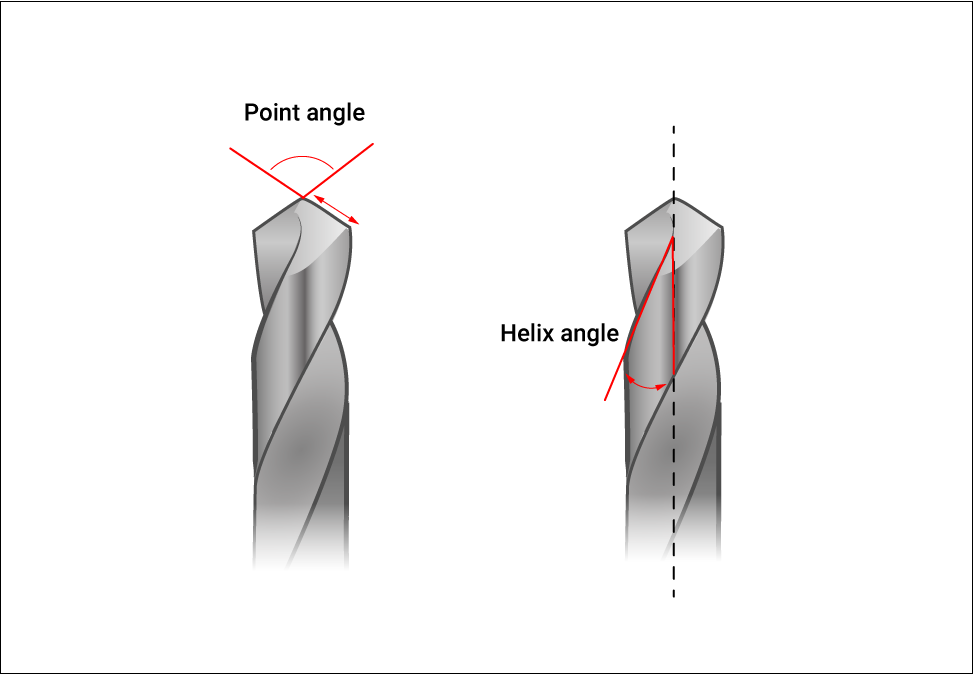
The CNC drill machine
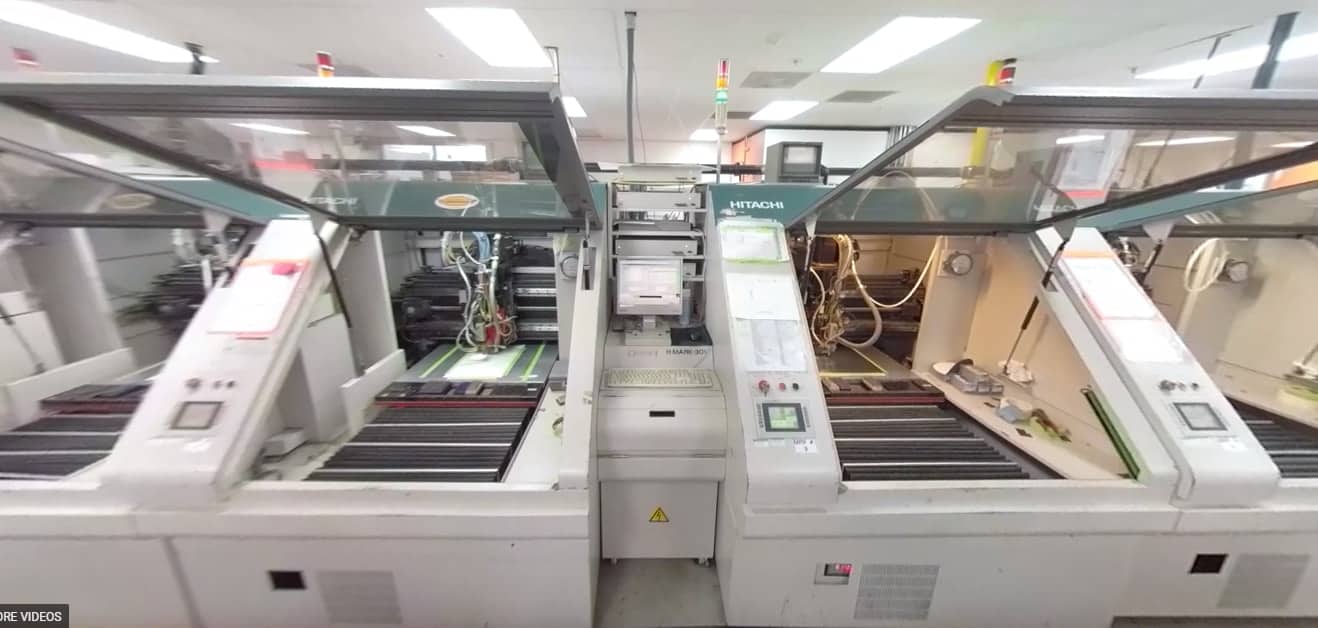
The drilling machine is a preprogrammed computer numerically controlled (CNC) machine. The drill occurs based on the XY coordinates fed into the CNC system.
The spindles rotate at a high RPM to ensure an accurate drill hole is found on the board. When the spindle rotates rapidly, heat is generated due to the friction between the hole wall and the spindle.
This melts the resin content on the hole walls, resulting in a smear of resin. Once the required holes are drilled, the exit and entry panels are discarded. This is a small gist of what happens on the shop floor.
Unlike the etching and plating process, drilling doesn’t have a fixed duration. The drilling time varies on the shop floor depending on the number of holes drilled.
This is what happens behind the curtains in the circuit board manufacturing unit. To know more about computer-aided manufacturing related to PCB read What is CAM or computer-aided manufacturing?
Two significant aspects to be considered in the drilling process:
- The aspect ratio
- Drill to copper clearance (Drill to the nearest copper feature)
Aspect ratio
Aspect ratio is the ability to effectively plate copper inside the holes(vias). Copper plating of the interior part of holes is a tedious task when the diameter is decreased and the depth is increased.
This requires a plating bath with a high throwing power so that the liquid can gush into the tiny holes.
Aspect ratio (AR) = (Depth of the hole/ Diameter of the drilled hole)
The aspect ratio is 10:1 for through holes and 0.75:1 for microvias.
Typically, for a 62-mil PCB, the minimum drill size is 6 mil.
Drill to copper
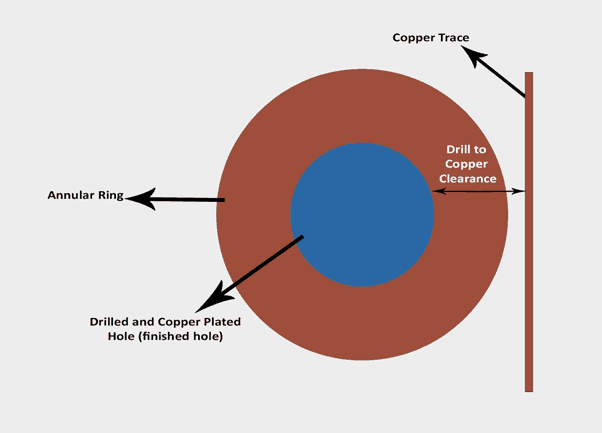
The drill-to-copper is the land clearance between the edge of a drilled hole and the nearest copper feature. The nearest copper feature can be a copper trace or any other active copper region.
This is the deciding factor since even a small deviation will lead to circuit disruption. The typical drill-to-copper value is around 8 mils.
Minimum clearance = annular ring width + solder mask dam clearance
Classification of holes
The drilled holes are classified into plated through-holes (PTHs) and non-plated through-holes (NPTHs).
The plated holes (PTHs) are the signal-carrying conductive vias that establish interconnection between the different layers in the circuit board.
The non-plated holes (NPTHs) are non-conductive. These are used to hold the components in position during the PCB assembly process. The component mounting holes are NPTHs. There is no tolerance level for these holes since the components won’t fit in if the hole size is too small or large.
A rule is a rule even for a hole
Drilling holes on a circuit board is not as easy as it sounds. This requires great precision and should adhere to certain design rules. Let us have a look at these requirements for NPTH and PTH.
Non-plated through-hole (NPTH)
- Finished hole size (minimum)= 0.006″
- Edge-to-edge clearance (from any other surface element) (minimum)= 0.005″
Plated through-hole (PTH)
- Finished hole size (Minimum) = 0.006″
- Annular ring size (Minimum)= 0.004”
- Edge-to-edge clearance (from any other surface element)(minimum) = 0.009″
Drilling disasters
After repeated usage, drilling tools tend to wear and break. This leads to the following problems:
The accuracy of the hole location is compromised
The accuracy is compromised when the drill bit fails to hit the preferred spot and shifts away in the same axis. The shifts in the drilled hole will give rise to tangency or breakout in annular rings.
Roughness inside the drilled hole
Roughness leads to a non-uniform plating of copper. This results in blowholes and barrel cracks. It can also result in lower insulation resistance due to the penetration of copper plating solution to the hole wall.
Resin smear
The resin in the board melts due to the heat generated during the drilling. The resin sticks to the hole walls and is called a resin smear. This again results in poor copper plating and leads to conductivity failure between the via and the interior layers of the circuit. The resin smear is removed by a chemical solution.
Presence of entry and exit burrs
Burr is the unwanted part of copper sticking out of the hole after the drilling process. They are mostly seen both on the top surface and bottom surface of the printed circuit board stack-up.
Nailhead
If the nailheads are improper, then there is a chance of copper bends in the inner layers while drilling. These copper bends cause uneven plating and result in conductivity issues.
Delamination
The partial separation of the circuit board layers is considered delamination. Improper drilling causes delamination.
All these irregularities ruin the board’s integrity, which has been a nightmare for the manufacturers. For these reasons, our in-house design engineers whimsically define PCB as “problems come back!”
In order to eliminate these flaws, scholars have researched the drilling process and design structure and have come up with the following solutions:
Remedies
Desmear process: It is a chemical process where the melted resin deposited on the hole walls is removed. This process eliminates unwanted resin and enhances electrical conductivity through the vias.
Deburr process: It is a motorized process that eradicates the elevated ends (crowns) of the metal (copper) called burrs. Any debris left out within the holes is exterminated through the deburring process. The desmearing process is repeated after deburring.
Delamination: It can be avoided by using laser drills. As mentioned earlier, in laser drilling, the workpiece and the tool do not come under contact, thus eliminating delamination.
Take a look at the quick DFM guidelines below, which can help you save a few bucks.
DFM drill validation tips for PCB designers
- The aspect ratio must be kept to a minimum to avoid drill wear
- An increase in different drill sizes in the design ( having different hole sizes) will call for increased drill bits (drill bits will be changed for specific sizes). If you restrict the implementation of different drill sizes, it will cut down the drill time.
- Check
- If non-plated drills have connections
- For drill count/size between drill file and fab print
- If drill type is defined (PTH / NPTH)
- For close holes less than 0.006″, if yes, it must be addressed
- For mouse bites
- If the drills and other features on copper layers are falling outside the board profile
- If via sizes should be dropped to meet the minimum aspect ratio (A/R) requirement, looking at drill tolerance
- For plated drill tolerance less than +/- 0.002″ and for NPTH, drill tolerance of +/- 0.001
- Fab drawing for arcs showing NPTH drill/slot or cutout locations that are missing in the drill file
- For via filling requirement w.r.t. assembly guidelines
The drilling process has been optimized in recent years compared to earlier technologies. With the exponential growth in the circuit board industry, drill precision is reaching close to perfection.
We believe now you have a better picture of how the PCB drilling process is done. It looks quite complicated, doesn’t it? Don’t worry! Just submit your design files (Gerber) to Sierra Circuits. Allow us to drill while you sit back and relax.