Contents
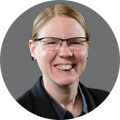
On-demand webinar
How Good is My Shield? An Introduction to Transfer Impedance and Shielding Effectiveness
by Karen Burnham
HDI PCB Case Study: When customers want to design HDI boards that are as compact as possible, there is often very little reliable guidance from the chip vendors. Heed the warnings of Texas Instruments: Consult board manufacturers from the start of any projects involving BGAs with a pin pitch of 0.4 mm and smaller.
Partner Early for HDI Board Design
Written by John Levreault and originally published in PCB Design Magazine
To preface this story about the design of my first HDI PCBs, let me point out I’m primarily an analog design engineer who’s been designing mixed-signal boards for well beyond 25 years. There’s nothing better than starting with a fresh sheet of paper, or more recently a blank screen, and developing a schematic that leads to a board that performs exactly as intended.
I think in terms of schematics. Over the years, by the way, I’ve designed many high-power class-D amplifiers that are in wide use, with varying amounts of logic to support or control that function. Today, though, chip vendors have made custom design unnecessary, for the most part, for amplifiers with outputs up to 250 W or so. More power to them (!) and hats off, but I do have a bone to pick with them in another regard. I’ll get to that soon.
The first project I was contracted to design, which led, inevitably, to an HDI board architecture, was a multimedia processor based on a Texas Instruments OMAP. It was an upgrade of a product for which there was a lot of existing hardware and legacy peripherals, and my customer wanted to move to a new processor for improved audio and video performance and speed, but still use the peripherals that had been designed generations ago. There was a great deal of I/O: multiple USBs, WiFi, and much more. It was, in simple terms, a hub.
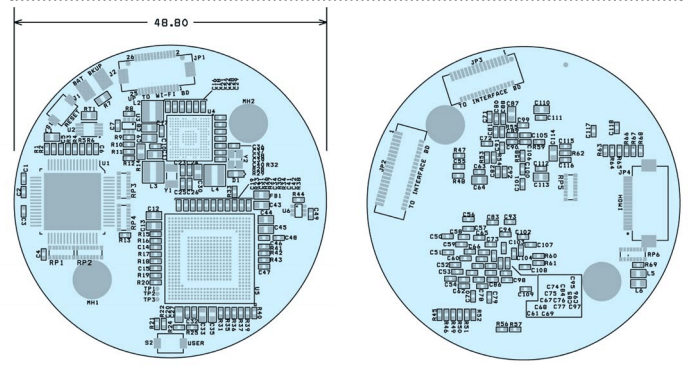
OMAP processor (lower right quadrant), its companion power-management chip (upper right quadrant)
that drove the stackup, and a video-processing device on one side (a) with connectors and many of the
passive components on the other side (b).
The form factor was very small, only two inches in diameter.
Implementing all the required functions involved several boards in a stack spaced just 1 mm or so apart. Some of the cards were joined by board-to-board connectors; others that had tall components required a flex connection. There was an audio board, an interface board, a WiFi board – which were fairly conventional four-layer boards – and a central board designated the DSP board, incorporating the OMAP and its companion power management chip (TPS65950), as well as a video processor.
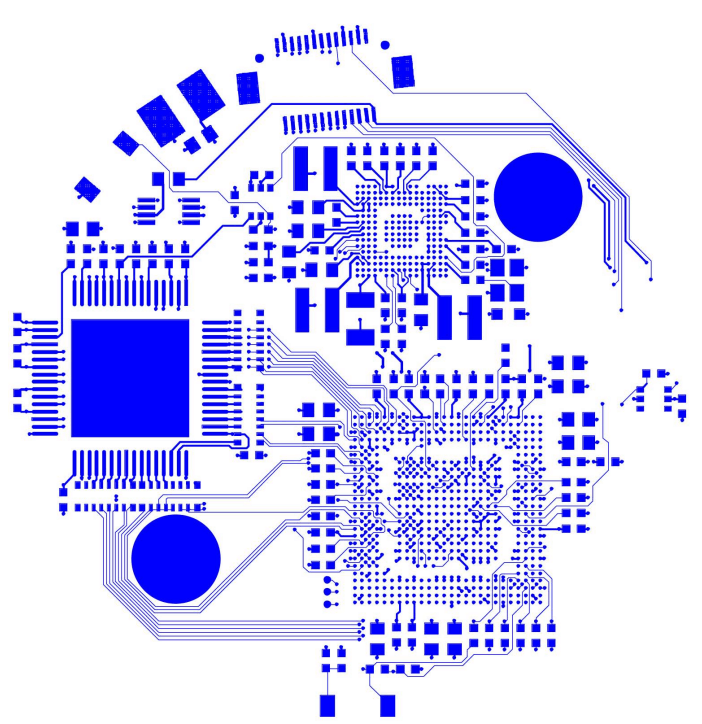
the pads for the device, which has a 0.4-mm pin pitch, though top-layer traces were navigated to a
few pins at the matrix perimeter.
The OMAP in this case is packaged in a BGA with pins on a 0.5-mm pitch.
Yet there was a more difficult routing challenge.
I knew no tactics to navigate traces from inside the pin matrix of the power-management chip, which has 209 pins on a 0.4-mm pitch. Clearly, this board layout would be an education. There’s no way to fan out from the center clusters of pins on such a tight pitch without resorting to vias in pads.
There are gaps among some of the pins along the matrix outer periphery through which I could fan out from some of the pins in the second row, and there is also a moat in the middle of the matrix that could have permitted me to use conventional vias for routing to some of the pins along its edges, but basically there is no practical way to get to most of the pins and route the board except for blind vias in pads.
Also read: The History of High Density Interconnect
Texas Instruments agrees.
I had the advantage of an open-source design, the BeagleBoard, whose documentation includes Gerbers and the Allegro file, so I could study the via stack-up stemming from an OMAP and other devices packaged in BGAs with a 0.4-mm pin pitch. And TI has some white papers with recommendations about what kind of board designs might work with this pin geometry, which describe a couple of options. But I suspect those responsible for the white papers didn’t actually design such boards. It’s what I call “armchair engineering.” However, they do make good points:
- The standard rules of thumb for board design do not apply when ball pitches of 0.4 mm or less are involved.
- “Close coordination and communication between the device supplier, the PCB designer, the board fabricator, and the assembly shop is mandatory” because “fine-pitch board design is a team effort.” (Reference 1)
Fortunately, I could learn a lot by essentially reverse-engineering an open-source design by which I was able to develop my via stack.
Even so, that was no picnic.
While I was designing the DSP board, which was eventually routed in six layers with microvias, buried vias and therefore multiple laminations, I didn’t know who would build it. I took to heart the admonition from TI and other quarters to immediately open a dialog with a manufacturer. Several shops said they could fab the board, but as discussions progressed, they either couldn’t do it or the way they planned to do it was too complicated.
A diligent search led me to partner with Sierra Circuits.
The company built the board and along the way advised me how to architect it to achieve the most efficient, manufacturable design. The decision to use microvias in 10-mil pads resolved my routing issues for both the PMIC and the OMAP for that board.
The next project I landed that would involve a BGA on a 0.4-mm pin pitch progressed more easily. I sought advice from my contact at Sierra Circuits who had helped me architect the first HDI board. This project, a wearable personal communication device, was less than half the size of the other board. The prototype had to be about 1 inch by 1.25 inch and include debugging and programmer ports, but the production version would be only 0.7 inch by 1 inch. My design was consolidated in six chips, so clearly the board had to be double-sided to contain those as well as a USB interface, all the passives, and some additional elements. This was a battery-powered system, so it also needed a charger interface.
Also read: 9 HDI Considerations for Manufacturability and Cost
Obviously, I had to find the smallest packages available.
For the MCU, my options included QFNs and the BGA I selected, whose 80 pins have a 0.5-mm pitch. The available BGAs for another device, which has only 51 pins, include one with a 0.65-inch pin pitch and a smaller one with a 0.4-mm pitch. The one with the looser pitch would not fit on the board, so I had no choice but to use the BGA with the 0.4-mm pitch, and it was that package that drove my stack-up. There is a third major component in a QFN, and I also used a QFN for my power-management device. The board also carries some flash memory in a really big package. Most of the passives are 0402 capacitors and there are two 0603 bulk capacitors.
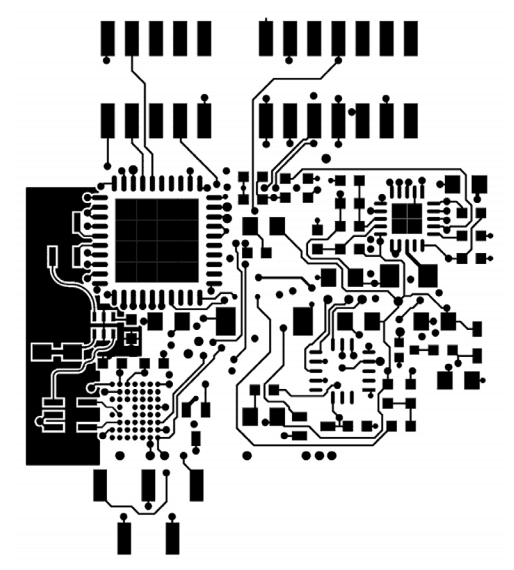
0.4-mm pad pitch – onto a double-sided board whose long dimension is
just 1.25 in. The top signal layer is shown.
My contact and I worked out a routing strategy resulting in a six-layer.
It was a double-sided board – signal, ground, signal, signal, power, and ground – with microvias from layer 1 to 2, 1 to 3, 6 to 4, and 6 to 5, and a standard via from layer 1 to 6. I embedded local copper pours into the inner routing layers to aid power distribution It was manually routed, using Cadence OrCAD Layout Plus. The scheme enabled me to put the two BGAs on opposite sides of the board: the MCU on the backside, center top, and the BGA with the 0.4-mm pitch on the topside, lower left.
For the most part, I was able to keep the chips on one side of the board from overlapping those on the flip side. There was a Bluetooth chip, which made sense to locate next to the antenna along a board edge. There was a requirement to put the USB interface, which is also the charger port, in a particular spot, so that told me where to put the power-management chip.
I needed five or six different supply values for the digital devices and a supply for an analog device.
Everything has a common ground. Rarely do I split planes for ground. I use ferrites and bulk capacitors for isolating the Vcc or Vdd supplies from the bulk supply running through my power plane. I prefer to route power nets last and route the top signal layer first, which completes much of the job. It’s easier, I find, to nudge a signal trace to make room for a power via rather than the other way around. But if you ask 10 other people you’ll get a dozen other opinions. The trick is placing components to minimize the rats’ nests of routing.
Though the BGA with the 0.4-mm pitch has 51 pins, I needed only 26 of them, five of which are connected to the debug port in the prototype. Regarding the 80-pin MCU, six pins had no function but I routed them to a debug port just in case. The project was designed for a customer offshore who is still in development, so having those available should be handy. Permit me to return to my issue with chip vendors. The use of HDI board architecture in my experience is driven by the presence of BGAs with a 0.4-mm pin pitch. Even tighter pitches are soon to follow. I think the companies that build the dense chips that need such packaging should have real documentation about real things that have been built with those products.
Certainly, the designers who create those chips with internal clock rates in the hundreds of MHz want to avoid compromising signals.
So things are not necessarily placed in locations on the die that would result in the most convenient pinouts for customers. The evaluation boards that are provided are not usually architected for very tight packing; they’re designed so customers can easily get to test and debug points.
But at the end of the day, when customers complete development and want to design boards that are as compact as possible, there is very little reliable guidance from the chip vendors. Take my advice and the recommendation from TI: Early in the HDI design process, partner with a board manufacturer who knows what to do.
References
1. Texas Instruments Application Report SPRAAV1B
The author
John Levreault is the president of Orvelle Technologies in Boxford, Massachusetts. He specializes in the design, development, and production of custom analog and mixed signal products for OEMs. He can be reached via john@orvelle.com.
For more information on design rules, check with our DESIGN SERVICE team.
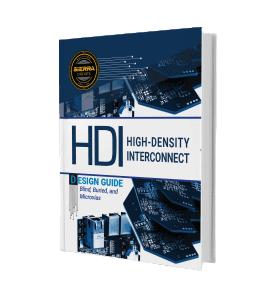
HDI PCB Design Guide
5 Chapters - 52 Pages - 60 Minute ReadWhat's Inside:
- Planning your stack-up and microvia structure
- Choosing the right materials
- Signal integrity and controlled impedance in HDI
- Manufacturing considerations for higher yields