Contents
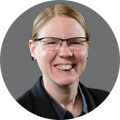
On-demand webinar
How Good is My Shield? An Introduction to Transfer Impedance and Shielding Effectiveness
by Karen Burnham
Why IPC-2581 is the go-to standard in PCB manufacturing? Similar to the Mentor Graphics-owned ODB++ in terms of functionality, it takes the lead over its competitor for it is open and neutral. And when it comes to good ol’ Gerber, it might just be time to retire.
What is IPC-2581?
The IPC-2581 standard defines a format for organizing and conveying printed circuit board designs from CAD tools to CAM systems for fabrication and assembly. The standard consolidates all aspects of a design, from layer descriptions through assembly and test details, into one file in one data format.
Why IPC-2581?
It is easy to say that IPC-2581 is open and neutral. But how open and neutral is it really? Released in 2004, the new data and transfer methodology promised to offer a smoother CAD-to-CAM data exchange process without human intervention.
Circuit board design comes with its share of files. And we’re talking about a lot of files to deal with: Netlist (IPC-356D), Excel and JPEG, Drill (Excellon), Artwork (Gerber RS274X), Readme files of notes and instructions, and so on.
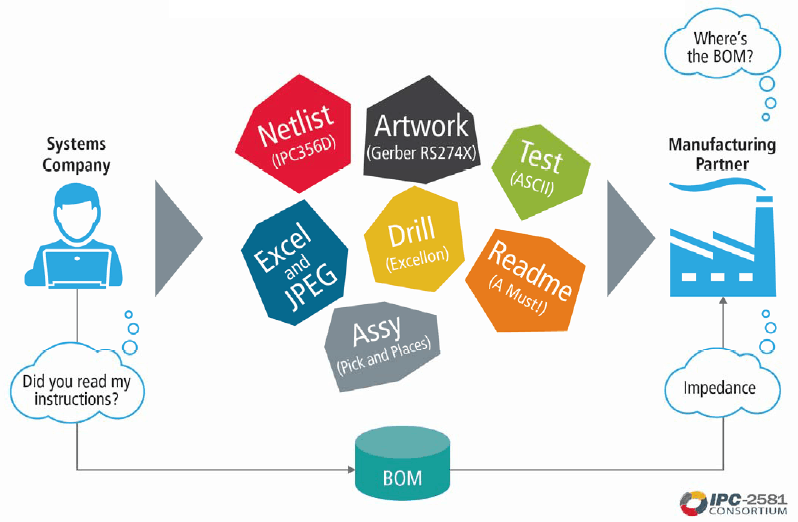
Most PCB designs are exported to manufacturers as a series of Gerber files that graphically describe the layers, combined with a drill file, a netlist, a board drawing, and a file of various notes and instructions. A bill-of-materials file and a file of coordinate data to drive pick-and-place machines are also included for assembly operations. None or a few of those files except for the Gerber files share a common format. They are simply aggregated, compressed, and sent to the manufacturer to interpret.
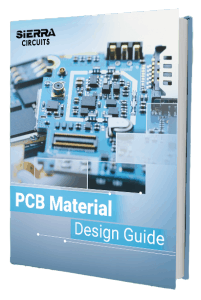
PCB Material Design Guide
9 Chapters - 30 Pages - 40 Minute ReadWhat's Inside:
- Basic properties of the dielectric material to be considered
- Signal loss in PCB substrates
- Copper foil selection
- Key considerations for choosing PCB materials
Download Now
When the conglomerated files arrive at the manufacturer, the staff first must identify the order of layers because, among Gerber files, there is no convention on the design side for layer names, types (plane, signal, solder mask), or polarity. That typically consumes a quarter-hour. If there is any uncertainty about how the layers are designated as received, the job must be sidelined until the designer can be reached for confirmation. When the layer order is resolved, the Gerber files and the information in the accompanying files must be translated to the format recognized by the fabricator’s CAM system, which is almost universally ODB++.
Valor Computerized Systems developed the ODB++ format two decades ago so that design data could be output from CAD platforms as a uniform hierarchy of files that could be downloaded and read directly by the CAM systems the company sold to PCB manufacturers. ODB++ can present a much richer description of a design than Gerber files can provide and eliminates the delays inherent with Gerbers because all the design files share a common format that requires no conversion to program production controls. Mentor Graphics acquired the company a few years ago and continues to market Valor CAM software.
PCB designs can be output in the ODB++ format from most CAD tools, not only those from Mentor Graphics. Nonetheless, Gerber-based design export remains the industry default by force of habit. Despite the advantages of ODB++ for design transfer, some CAD vendors have recently worried that their implementation of that format may become captive to future proprietary restrictions by Mentor Graphics, though there is no evidence at this time the firm intends to impose any such constraints. That uncertainty is responsible for the revitalization of the open-source standard IPC-2581, which in its original form was very similar to ODB++.
As a PCB designer, why should you care about whether your manufacturer receives your design in one or a thousand files, as long as it is sound and thorough? More files mean more work and more work means more chances to make mistakes. When gathered in one single file, you can effortlessly import your design, augment it, and export it by any business system throughout the value chain. As simple as one single file: This is the intelligent part.
This open standard, which is free for implementation by any software developer, incorporates extensive attributes to pinpoint exactly what designers intend manufacturers to build. At some level of circuit complexity, you might want to consider opting for a highly organized and efficient means of exchanging data with your fabricator, therefore reducing the margin of error on both sides of the handoff.
IPC-2581 consortium
As a Consortium member, Sierra Circuits endorses the IPC-2581B standard, which will accelerate manufacturing and assembly. It will enable design data to be downloaded without interpretation directly into CAM systems, thereby saving time and labor, compared with Gerber-based projects. Whether the industry embraces this intelligent format hinges on how faithfully the vendors of CAD tools, DFM software developers, and CAM system developers implement it. The first releases under IPC-2581B are anticipated in 2014.
All the way down to the factory floor
Consortium member Hemant Shah explains the vision IPC had when members started working on the new standard, “The bottom line is the handoff of OEM to manufacturers. This is where we focused most of our attention so far because this is the problem that we wanted to solve. The vision was that IPC-2581 goes all the way to the machines that the manufacturers have, all the way down to the factory floor.”
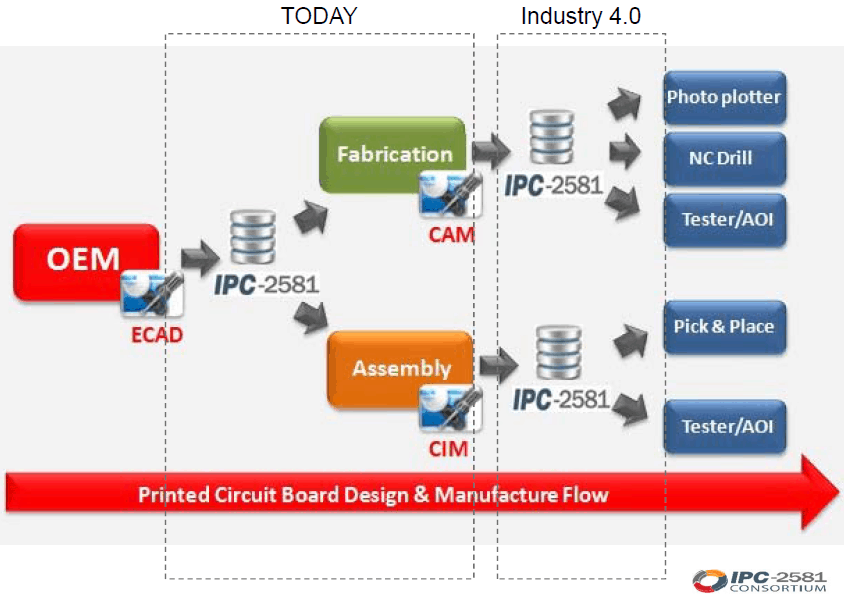
IPC has a standard called CFX – which stands for connected factory exchange – that passes machine-specific data to different machines. That is one task designers don’t have to worry about. If you have a Pick-and-Place machine, all you need is the parts the machine needs to work on. This data for the pick-n-place machine will go to the machine in IPC-2581 format.
IPC-2581 is an IPC standard. Nobody owns it, everybody can implement it; thus comes the open part. The Consortium developed this IPC standard in 2004 in an effort to combine the best of ODB++X – which does no longer exists – and GenCam.
The limitations of Gerber-based design transfer
- A mix of files in different formats, which are incompatible with PCB manufacturing software
- No convention for designating layers
- Data can be misinterpreted
The advantages of IPC-2581B
- All the data within a design can be exported in one file, in one format, from a CAD tool directly to a manufacturer’s CAM system
- No intermediate data translation is required
- Eliminates human errors
- An open standard free from proprietary restrictions
How does revision B extend the standard?
- Improves description of build intent with provisions for stack ordering, material types, technology attributes, stack-up composites
- Expands BOM section to include stack-up
- Includes geometry object fill types, line types, user-defined primitives
- Back-drilling support
- Pin-one origin/orientation standard criteria
- Pad-stack reference definitions
- Z-axis definition, V-groove cavity/slot support
- More notes on design intent can be added in the Spec section
Join the consortium to promote IPC-2581
- Ask your company to become a corporate member
- You can join personally as an individual associate member
- Visit www.ipc2581.com to join
The first IPC-2581 PCB
Even though the format was released almost 15 years ago, the first IPC-2581 circuit board was only fabricated in September 2012. The bare board was fabricated with a PCB design from Fujitsu Network Communications, which exported the fabrication data from Allegro. The communications equipment company announced that it reduced the overall fabrication preparation time by 30 percent.
Interestingly enough, it is around that time that Mentor announced that it supported its rival standard. Currently, many other tool providers support IPC-2581: We can name Altium, Cadence, Zuken, Siemens, Polar Instruments, Adiva, Wise Software… This is a clear hint that the neutral XML-based standard is a must-have.
ODB++ users will love it: IPC-2581 offers all the advantages of the Mentor format without requiring its users to get a license. It was made to serve Industry 4.0.
The use of IPC-2581 in Industry 4.0
Michael Ford, Marketing Director at Aegis Software Corporation and member of the IPC-2581 Consortium, believes that the standard is now a key focus of interest. As he told us, “I’m very much into promoting smart factory operation Industry 4.0 for the future.”
However, Michael Ford continued, “It’s often neglected about what is needed from the design side in order to make Industry 4.0 possible. Because you actually can’t do Industry 4.0 unless you have a method of getting data from design through to manufacturing extremely quickly and without any mistakes.”
100% productivity
The normal operation of a factory will become very inefficient in doing that because the product line rate will never match customer demand. To help you picture this, we are going to use the example Michael gave us: If the customer demand is 800 and the line capability is 1000, you have lost 20% productivity. But the manufacturer has to have the 1000 capability in case the customer changes their mind. It takes so long with legacy engineering methods to move a product from one line configuration to another that it is simply not done. Manufacturing accepts that loss.
Manufacturers no longer have to accept that loss in Industry 4.0. “If the customer says they want 800 today, then the product is moved to a line that runs at 100% efficiency, making 800. And the faster line will be assigned to another customer.” Products are moved from one configuration to another configuration very quickly.
IPC-2581 allows the creation of a digital product model within one file. In their engineering systems, manufacturers can choose the line configuration for today and create the necessary data for those machines. “In the past, you would have different files, pictures, drawings, etc., Michael Ford stated. You would give them all to the various machine vendors. And you would say, ‘You do this. You do this. You do this.’ and talk to each other and try and get it done.”
This method would take at least a few days to have a program under the line ready to run. There simply was no day-by-day method. IPC-2581 resolves this issue since “having a single product model into a digital manufacturing engineering engine then allows you to choose the configuration day by day or even hour by hour.”
It indeed only takes a few minutes to convert that digital product data into a running SMT line.
Towards paperless operation
The strong suit of IPC-2581 is the fact that a single file contains the data for all of manufacturing. Now, what about the various elements that different machines will require? Like the location of components, component shapes and geometries, test points, and so on? Michael Ford says “it is kind of a translation.” Manufacturers choose which machine in the line will perform each task and then allocate the data accordingly. “But what you mustn’t forget is that the line isn’t only machines. There are people also doing manual assembly operations.”
The IPC-2581 file exported using EDA tools includes the base information with which to create documentation. For instance, when manufacturers assign jobs to manual operators – which in a modern factory will be a paperless operation – videos, for example, will show them exactly how things are done. Manufacturers have to make sure that they reference the exact design intent as part of that documentation. By offering the same consistent data, IPC-2581 puts an end to the document confusion that manufacturers had to deal with in the past.
Why do manufacturers support IPC-2581?
It makes sense that some PCB designers may still be reluctant to use IPC-2581. Just like they were when OBD++ came around and they had the choice to move on from Gerber. To tell you the truth, as a PCB manufacturer, we still receive 80% of our customers’ designs in Gerber. How can we convince them to use IPC-2581 when they even haven’t switched to ODB++ yet?
At Sierra Circuits, we have already fabricated circuit boards imported with IPC-2581. What is the difference with the other circuit boards, you may ask? Our front-end CAM engineers appreciate the simplicity of digital communication for more productive direct process engineering tasks. With Gerber files, they have to interpret how the data is expressed – whether this is in English units or metric units, for instance. The layer renaming, as well as the type and polarity defining, are also some of the arbitrary decisions they have to take according to our protocol.
We estimated that it takes about 15 minutes per job just to identify the order of the layers. Sure, it doesn’t seem so bad to put it this way. Now, multiply these 15 minutes by 120 orders that we receive on a daily basis. It is getting worse. Plus, if our operators make a mistake, then we have to deal with scrap. If the PCB designer makes a mistake, then we have to send the bill to the customer. Both scenarios are bad.
IPC-2581 allows our front-end team to easily output projects from CAD tools, avoiding having to put jobs on hold because of data uncertainty due to disparate formats. This also benefits our customers bypass delays in production and get their prototypes faster.
Customer testimonials
Speaking of our customers, one of them who has recently requested a quote for a board using IPC-2581 explained that the syncing between the output and the database motivates him to use the IPC standard. Michael Edwards, a Senior PCB Designer at Glenair, said, “With Gerber, it is possible to generate separately and at different times, and I have seen when it is not possible to know what database made what files. With IPC-2581 using the (free) WISE viewer it is very easy to check the output. The file also includes all the net lists and part information. I know people like the ODB++ tar ball, but it is just another ZIP file full of many files. For me, IPC-2581 is the best format.”
Another consumer electronics customer who was designing for controlled impedance confirmed that statement. He found the exchange with us very convenient. Instead of having to re-enter the data in different tools, he was able to use the stack-up data available in IPC-2581.
You can understand why your quick-turn manufacturer advocates the use of an open and intelligent format that eases the CAD-to-CAM transfer and therefore save both time and money.
Sierra Circuits has been supporting IPC-2581 for a while now and we will continue to do so. We encourage our customers to try it once; it’s all it takes to adopt it! We currently fabricate and deliver more than 10,000 circuit boards each month. If 50% of our orders get to us through IPC-2581, we estimate that we will be capable of shipping 15 percent more PCBs. And again, we are not the only ones taking advantage of this innovation. You will save money because we will spend less time working on your boards. IPC-2581 is a win-win situation for both fabricators and customers.
Read our article about IPC class 2 vs class 3: The different design rules.
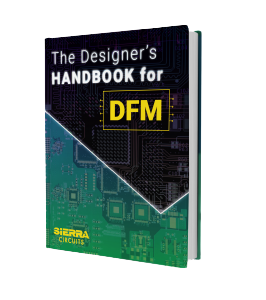
Design for Manufacturing Handbook
10 Chapters - 40 Pages - 45 Minute ReadWhat's Inside:
- Annular rings: avoid drill breakouts
- Vias: optimize your design
- Trace width and space: follow the best practices
- Solder mask and silkscreen: get the must-knows
Download Now