Contents
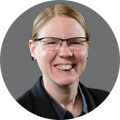
On-demand webinar
How Good is My Shield? An Introduction to Transfer Impedance and Shielding Effectiveness
by Karen Burnham
Humanoid robotics PCBs enable communication between sensors, actuators, and AI processors, a critical factor in building advanced robots. As robotics technology evolves, high-density, flexible, and thermally efficient boards play a key role.
In this article, you’ll learn the prerequisites for designing a humanoid circuit board and the advanced manufacturing techniques.
Highlights:
When designing printed boards for humanoids:
- Select high-frequency flexible materials like DuPont Pyralux TK and Panasonic FELIOS R-F775.
- Use flexible printed circuits (FPC) to integrate cameras, sensors, and AI processors for facial recognition, environmental awareness, and real-time decision-making.
- Incorporate rigid-flex PCBs to provide structural support and flexibility, aiding in smooth motion, balance, and terrain adaptation.
- Integrate microcontrollers/microprocessors in the main circuit board to process sensor data, run AI algorithms, and control actuators in real-time.
Humanoid PCB robotics market insights
The market for humanoid robot PCBs is growing rapidly, driven by advancements in AI, robotics, and miniaturized electronics. Below are key insights on leading manufacturers, market size, and growth projections.
Humanoid robot manufacturers
Humanoid robot manufacturers | |
---|---|
Manufacturers in the U.S. | Manufacturers in China |
Boston Dynamics | Unitree Robotics |
Agility Robotics | Deep Robotics |
Figure AI | Agibot |
1X | Ecovacs Robotics |
Tesla | Rokae |
Apptronik | Beijing HRIC Robotics |
Market size and growth projections
Global humanoid PCB market size
The global humanoid robotics circuit board market was valued at USD 4.40 billion in 2024 and is expected to reach USD 15 billion by 2030, growing at a CAGR of 22.2% from 2025 to 2030.
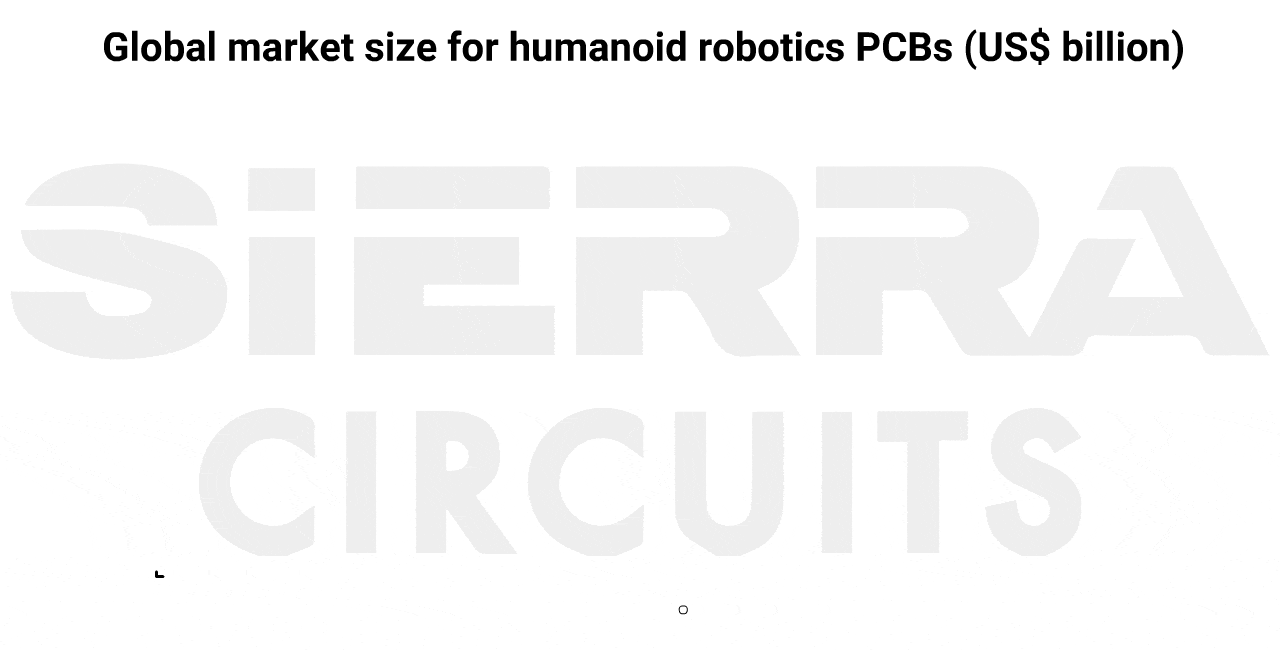
Humanoid robotics PCB market size in the United States
The U.S. humanoid robotics PCB market was valued at USD 1.75 billion in 2024 and is expected to reach USD 7.91 billion in 2030. The market is forecasted to grow at a CAGR of 21.7% from 2024 to 2030.
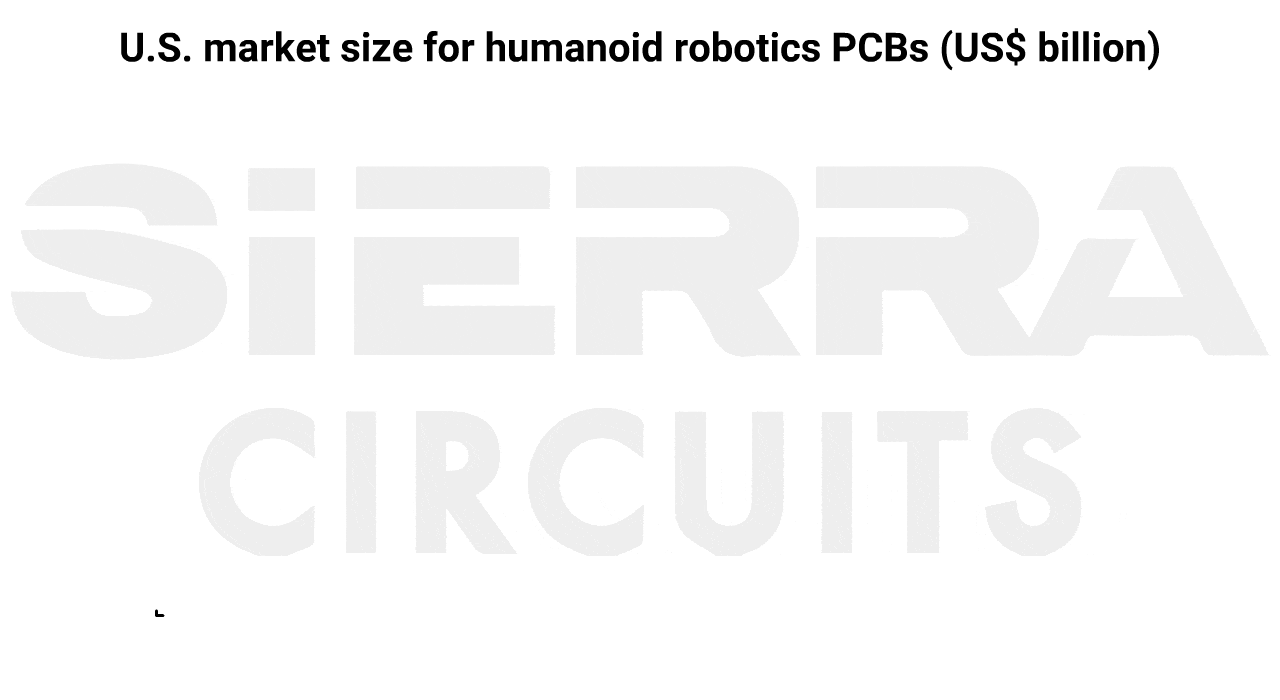
Humanoid robot PCB design market size
The U.S. humanoid robot PCB design market was valued at USD 1.15 billion in 2023 and is projected to reach USD 1.7 billion by 2030, reflecting a CAGR of 5%. Globally, the market was valued at USD 2.86 billion in 2023 and is expected to grow to USD 4.49 billion by 2030, with a CAGR of 5.8%.
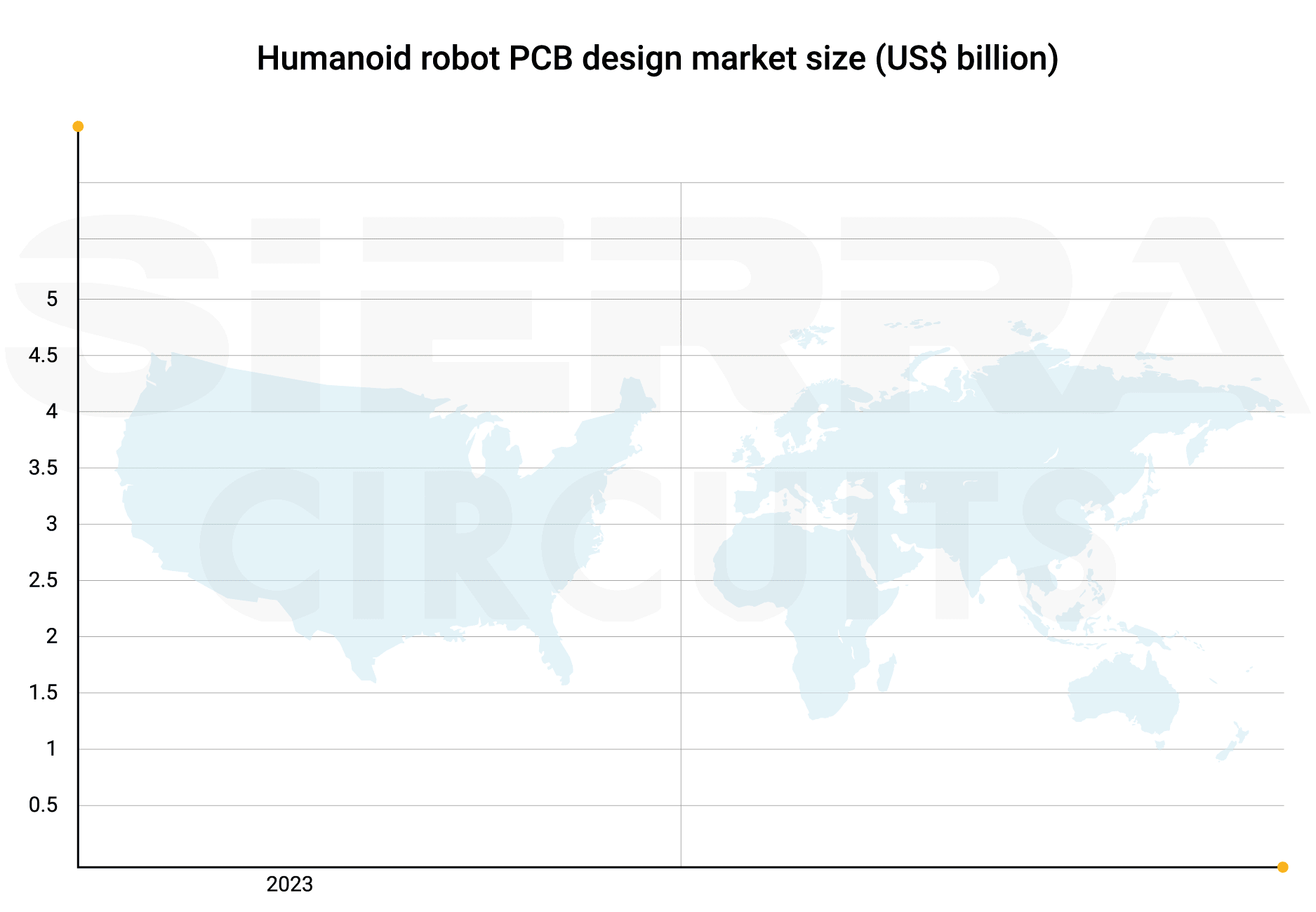
The global humanoid robot PCB design market is expected to witness significant expansion, with Europe leading at a CAGR of 6.9% and an annual growth rate of 7.3%. Innovations in high-density interconnect (HDI) PCBs, flexible circuits, and embedded components are key drivers of this increasing demand.
Source: Sierra Circuits’ market research analysis report.
Key industries utilizing humanoid robots
The humanoid bot market is experiencing growth across multiple sectors, driven by advancements in AI, automation, and IoT.
- Military and defense: They enhance security and efficiency by aiding in search-and-rescue missions and conducting surveillance in hazardous areas.
- Manufacturing and logistics: They improve workforce flexibility by performing dangerous or repetitive tasks and ensuring quality control through AI-driven defect detection.
- Home assistance and personal use: Growing consumer interest drives demand for robots that handle household chores and provide security monitoring.
These advancements highlight the increasing integration of robotics into daily life.
How PCBs help humanoids sense, think, and move
Humanoid circuit boards integrate advanced sensors, processors, and motor drivers that enable them to sense, process information, and execute precise movements.
Robots rely on coordination between sensing, processing, and actuation to function effectively. Their controllers continuously process high-speed sensory data, analyze internal states and surroundings and determine the best course of action.
Once a decision is made, they trigger motors, pneumatics, or other actuators to execute precise movements. This adaptive control loop allows them to respond intelligently to dynamic environments.
Traditional rigid PCBs are often impractical for confined spaces, particularly in joints and curved surfaces, where movement and flexibility are critical.
Flex and rigid-flex PCBs address these limitations by allowing circuits to conform to the robot’s form factor, ensuring continuous electrical interconnections while reducing bulk and mechanical stress. This makes humanoids lighter and ensures reliable performance even during dynamic movements.
When these boards work in harmony, humanoids can navigate complex spaces, react in real-time, adjust behaviors, recover from errors, and optimize performance—often improving through machine learning.
A prime example is Sophia, one of the most advanced humanoid robots known for its lifelike interactions. In 2017, it became the first robot to receive citizenship granted by Saudi Arabia.
6 key humanoid PCB design considerations
1. Incorporate HDI and fine-pitch technologies to save space
Humanoid robots have limited internal physical space, so printed boards must have a lower form factor while maintaining high functionality.
By leveraging high-density layouts, multi-layer boards, and fine-pitch components, you can save space. Custom-shaped PCBs fit into curved enclosures, aligning with the robot’s limbs, torso, and head.
To make the most of tight spaces, you can use vertically stacked multi-board setups like mezzanine or sandwich structures. This model stacks circuit boards vertically without increasing the overall form factor.
Flexible printed boards are also ideal for joints and moving parts, enabling smooth electrical connections in confined areas.
A modular PCB design approach simplifies assembly, maintenance, and future upgrades, allowing individual PCB modules to be replaced or improved without altering the system.
2. Use high-speed interfaces to integrate PCB subsystems
A humanoid robot relies on various subsystems, including sensors, actuators, microcontrollers, and communication interfaces.
Implement appropriate protocols based on speed and use case. Utilize high-speed communication protocols like SPI to connect critical subsystems, such as motor control and IMUs, where low latency is essential. Opt for I2C in sensor integration, where speed is less critical but efficient multi-device communication is required.
Strategic power distribution, data routing, and efficient PCB component placement minimize latency in real-time robotic functions.
3. Adopt thermal and shock-resistant techniques to withstand vibrations and stress
Humanoid robots operate in dynamic environments, facing constant mechanical vibrations and thermal fluctuations. With AI processors and motor controllers generating significant amounts of heat, efficient thermal management is essential to prevent overheating and ensure continuous high-performance computing for real-time robotic decision-making.
Use high-quality advanced materials (DuPont Pyralux TK and Panasonic FELIOS R-F775). In addition to this, implement PCB thermal management solutions such as thermal vias, plated through vias, and thermal via stitching techniques to maintain optimal operating temperatures.
Further, implement metal-core PCBs to ensure temperature-sensitive components remain stable under continuous operation.
By integrating high-ductility solder materials like SAC305, the risk of microcracks in solder joints, especially in high-vibration areas (near motors), is minimized, preventing component detachment. Additionally, tear-drop routing helps mitigate flexural stress on PCB traces, preventing cracks and peeling in critical pathways.
To further reinforce structural integrity, circuit board stiffeners can be used to provide mechanical support to flexible PCBs. Finally, incorporating rubber or silicone dampers between joints and sensitive components helps absorb shocks and vibrations.
Conformal coatings (silicone and polyurethane-based) and protective IP-rated enclosures (e.g., IP54, IP67) shield the board from dust, moisture, and mechanical wear.
4. Place PCBs close to sensors and motor to avoid transmission delays
Stable signal transmission is crucial, especially in high-frequency circuits, where any discrepancies can cause EMI.
Humanoids rely on real-time data from IMUs, force/torque sensors, and vision systems—any delay or corruption can cause instability or falls. Further, motor control signals (SPI, EtherCAT) must be precise to avoid jitter or lag in dynamic movements.
Placing PCBs close to sensors and motors is essential to reduce transmission delays and minimize signal attenuation. It also lowers susceptibility to electromagnetic interference generated by motors, actuators, and power electronics.
This proximity also helps prevent voltage drops and ensures that high-speed signals, such as real-time motor control commands, remain stable and accurate.
Impedance matching and differential pair routing help minimize interference and crosstalk. A well-designed PCB stack-up further reduces signal reflection and enhances signal integrity.
5. Implement power gating to prolong battery life
Efficient power management is essential for humanoid robots, which operate on multiple voltage levels to support sensors, actuators, and processing units.
DC-DC converters regulate voltage efficiently, reducing power loss and ensuring stable operation. Strategic placement of decoupling capacitors near ICs stabilizes voltage levels and minimizes noise.
Implement power gating to selectively shut down inactive sections of the robot, such as idle sensors or actuators, to prevent unnecessary energy drain. Microcontrollers and power management ICs regulate these circuits dynamically, minimizing standby power consumption and improving overall efficiency.
Motors are one of the largest power consumers in humanoid robots. Implementing smart motor control with PWM (pulse width modulation) ensures efficient speed by delivering only the necessary power. Regenerative braking captures and reuses energy when a motor slows down, reducing overall power consumption in actuators.
Since humanoid robots rely heavily on battery power, continuous battery health monitoring is crucial. Battery management ICs can track charge cycles, predict battery life, and prevent overcharging or deep discharging.
To build an efficient power delivery network, see 7 considerations for PCB power supply design.
6. Design for scalability to support future upgrades
As robotics technology evolves, printed boards must be designed with scalability in mind. Whether you’re designing a PCB prototype or looking for mass production, a well-structured design approach allows for future modifications.
Standardized connectors, flexible architectures, and modular subsystems facilitate easy transitions from development stages to commercial deployment without extensive redesigns.
To learn how to design a reliable flex PCB, download our eBook.
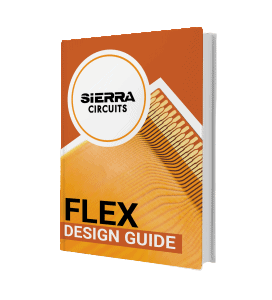
Flex PCB Design Guide
10 Chapters - 39 Pages - 45 Minute ReadWhat's Inside:
- Calculating the bend radius
- Annular ring and via specifications
- Build your flex stack-up
- Controlled impedance for flex
- The fab and drawing requirements
Download Now
Core PCB subsystems required for humanoid robotics
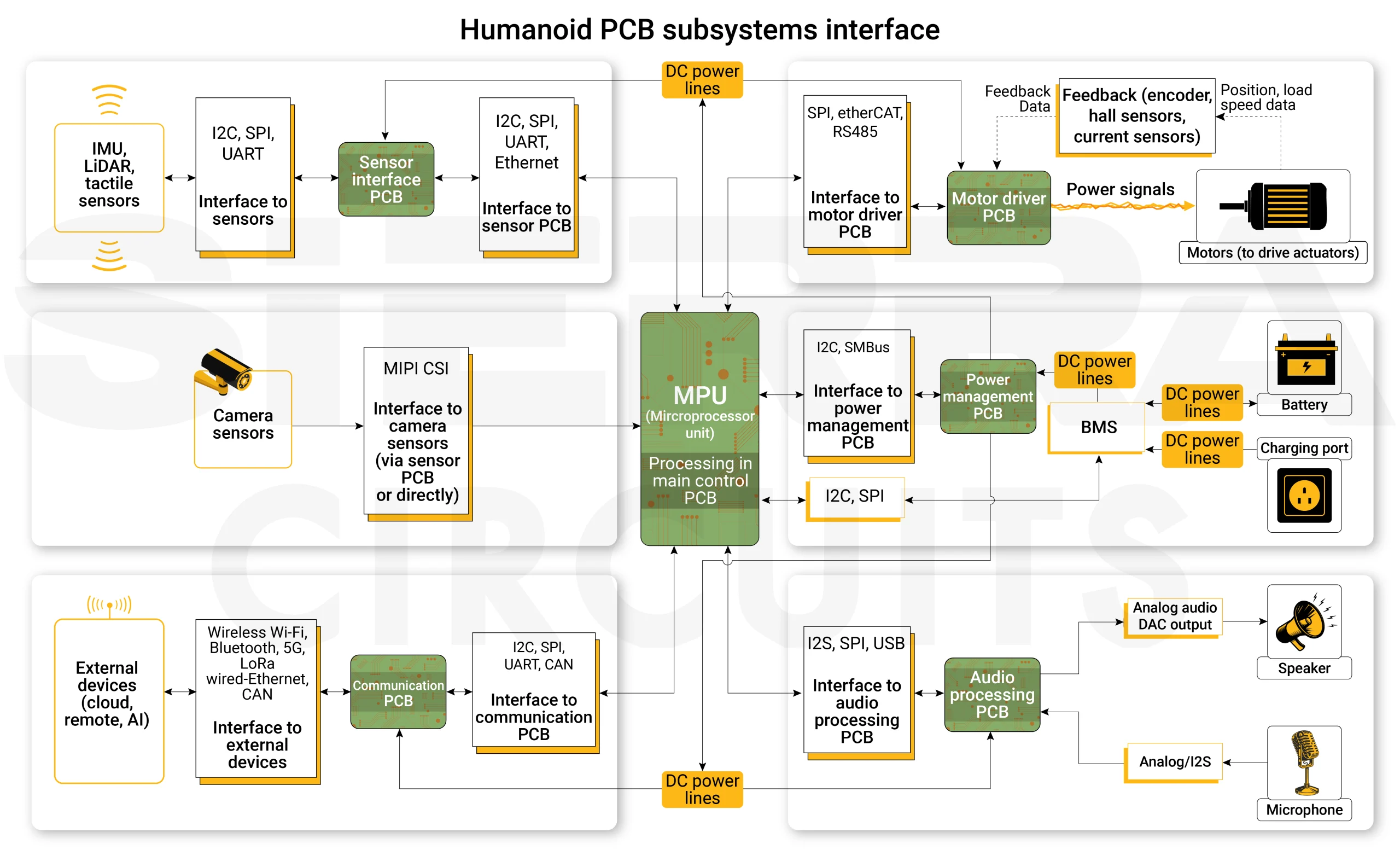
1. Control systems for real-time decision-making
The main circuit board integrates powerful microcontrollers or microprocessors to execute real-time processing, decision-making, and motion control. This board processes data from various sensors, runs AI-driven algorithms, sends precise control signals to actuators, and coordinates interactions with the environment.
2. Sensor interface for perception and awareness
A humanoid’s perception relies on dedicated sensor PCBs that interface with vision systems (cameras), spatial awareness sensors (IMUs, LiDAR), tactile sensors, and microphones. These boards enable accurate data acquisition and efficient transmission to the main control board for adaptive behavior.
3. Motor drivers for precision control
Every motion in robots is powered by servo motors, brushless DC (BLDC) motors, and stepper motors, all regulated by specialized motor driver PCBs. These boards ensure precise actuation, smooth movement, and coordinated limb articulation.
4. Power management PCBs for stable and efficient energy distribution
Power management circuit boards regulate voltage, distribute power efficiently, manage battery charging, and incorporate protection mechanisms to prevent overloads.
These boards balance power demands across actuators, sensors, and processors.
5. Communication modules for data exchange
Reliable connectivity is enabled through communication PCBs, which facilitate data transfer between internal components via CAN, UART, or SPI and enable external communication via Wi-Fi or Bluetooth.
6. Audio processors for voice interaction and sound recognition
For humanoids with voice interaction, dedicated PCBs manage microphone input and speaker output, ensuring clear signal processing for natural communication.
The table below outlines the key PCB subsystems in a humanoid robot, detailing their connections, functions, and interface types.
Subsystems | Connected to | Functions | Interfaces and protocols |
---|---|---|---|
Control systems | Sensors, motor drivers, power PCB, communication PCB | Processes data from sensors, runs AI algorithms, and sends commands to actuators via motor drivers. | I2C, SPI, UART, GPIO, CAN, EtherCAT |
Sensor interface | Main control PCB | Transmits vision, IMU, LiDAR, and tactile sensor data to the main control PCB for real-time processing. | I2C, SPI, MIPI CSI, UART, Ethernet |
Motor drivers | Main control PCB, actuators, power PCB | Receives PWM signals from the main control PCB, regulates motor power, and sends feedback on motor status. | PWM, GPIO, SPI, EtherCAT, RS485 |
Power management boards | Battery, main control PCB, motor driver PCB, communication PCB | Converts battery power to required voltages, ensures stable power distribution, and provides overcurrent protection. | I2C, SMBus |
Communication modules | Control PCB, external devices (remote control, AI cloud, sensors) | Handles internal data exchange and wireless communication for remote operation and networking. | Wi-Fi, Bluetooth, CAN, UART, SPI, Ethernet, 5G, LoRa |
Audio processors | Main control PCB, speaker, microphone | Processes microphone input, enhances speech recognition, and manages speaker output. | I2S, analog audio, SPI, USB |
Beyond these subsystems, some advanced humanoids use dedicated AI accelerators to handle tasks like deep learning-based vision, natural language processing, and reinforcement learning for motion adaptation.
The role of flex printed circuits in humanoid robots
Flex and rigid-flex PCBs are the backbone of humanoid robots. They integrate advanced technologies into compact, highly adaptable designs. These advanced boards enable lifelike movement, precise environmental perception, and real-time decision-making, bringing robots closer than ever to human-like intelligence and interaction.
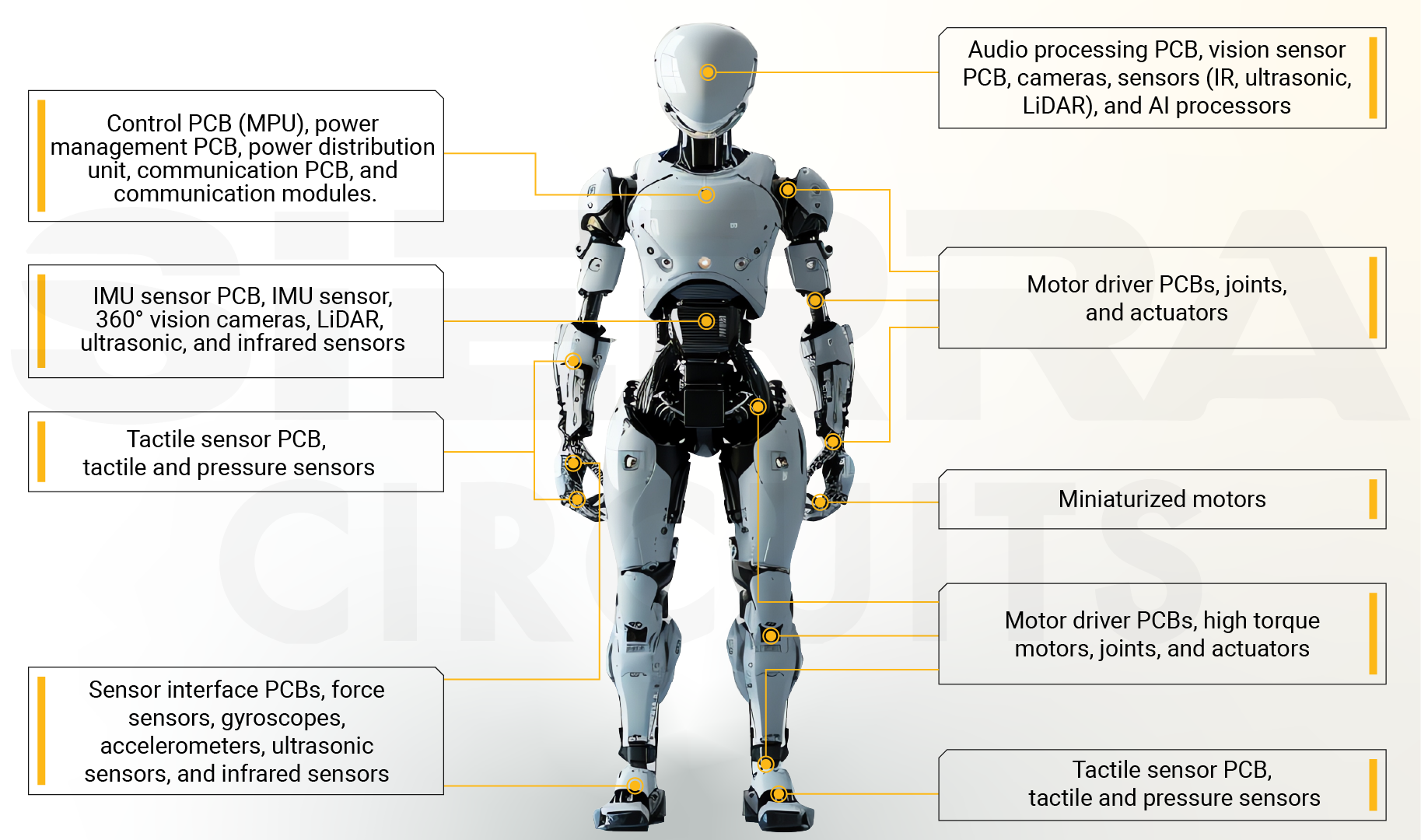
.
Robot anatomy | Function | Key components | PCB type and benefits |
---|---|---|---|
Head | Centralized information processing |
|
Flexible PCBs: Lightweight, adaptable, and allows seamless sensor integration for eye contact, facial expressions, and human-computer interaction. |
Torso | Structural stability and system coordination |
|
Multilayer flex PCBs: Supports high-density interconnections in limited space.
Rigid-flex PCBs: Combines robustness and flexibility for reliable operation. |
Arms and hands | Precision in motion and dexterity |
|
Flex PCBs: Provide flexibility for movement, reduce weight, and improve responsiveness for precise object manipulation and expressive hand gestures. |
Legs and feet | Mobility and balance |
|
Rigid-flex PCBs: Offer structural reinforcement while allowing flexibility, ensuring smooth navigation and balance across different terrains. |
Multiple locations | Perception and environmental awareness |
|
Flex PCBs: Enable compact sensor integration and efficient signal transmission for real-time environmental perception and interaction. |
Integration of flex PCBs with AI systems
AI is the brain of humanoid robots. It is responsible for real-time data processing, decision-making, and task execution. To keep up with these demands, artificial intelligence systems need high-performance circuitry. Flex PCBs play a key role by:
- Providing high-density connections for fast and efficient data processing.
- Supporting AI-driven learning and adaptation, helping robots improve their actions over time.
- Optimizing space and flexibility, making integration easier in compact robotic designs.
Sierra Circuits manufactures flex PCBs that withstand extreme bending (up to 200,000 cycles). Visit our flex PCB manufacturing capabilities to learn more.
Advanced materials and manufacturing techniques to build humanoid PCBs
1. Flexible and high-frequency materials
The use of advanced materials (DuPont Pyralux TK and Panasonic FELIOS R-F775) is revolutionizing PCB manufacturing for robotics. These materials offer significant advantages:
- Flexible substrates enable robots to achieve complex movements, enhancing their agility and adaptability.
- High-frequency materials contribute to miniaturization, allowing for compact yet high-performing designs.
Beyond these benefits, experimental applications of advanced materials open new possibilities in robotic design, offering improved thermal stability and enhanced resistance to harsh environments. These characteristics are particularly valuable in hazardous or extreme conditions, ensuring robots maintain reliable performance over extended periods.
Key manufacturing considerations for printed boards used in humanoids
- Ultra-thin flexible substrates allow engineers to develop highly maneuverable robotic components without compromising electronic performance.
- Polyimide-based substrates (e.g., DuPont Pyralux) offer excellent thermal and mechanical stability, making them ideal for flexible PCB fabrication.
- Rolled annealed copper is chosen over electrodeposited copper because of its superior ductility. It prevents cracking during repeated bending.
Rolled annealed copper offers superior ductility. - A protective coverlay shield circuits from environmental stressors and mechanical wear, further enhancing the bending endurance of the PCB.
- Liquid crystal polymer (LCP) based substrates offer low dielectric loss and high-frequency performance, making them ideal for high-speed data transmission in AI-driven robotics, radar, and 5G applications.
2. Nano-silver conductive ink printing for flexible circuits
Nano-silver conductive ink printing, commonly used in the additive manufacturing technique, allows for the direct printing of highly conductive traces on flexible substrates, eliminating the need for traditional PCB etching or laser direct imaging.
Key advantages of nano-silver conductive ink printing:
- Nano-silver inks can be printed on low-cost substrates, reducing overall material costs. It offers decent electric performance, making it a cost-effective choice for lightweight electronics.
- It is ideal for humanoid robotics, as it enables flexible and stretchable circuits that can withstand repeated bending and mechanical stress without cracking.
- Enables rapid prototyping of customized circuit layouts, improving iteration speed in robotic development.
While nano-silver ink printing is great for single and double-sided PCBs, it’s not the best choice for multi-layered circuits.
3. Advanced HDI with every-layer interconnect (ELIC) technology
HDI PCBs for robotics should be ultra-compact with complex interconnects. ELIC technology enables direct connections between multiple layers, reducing signal transmission delay and enhancing reliability.
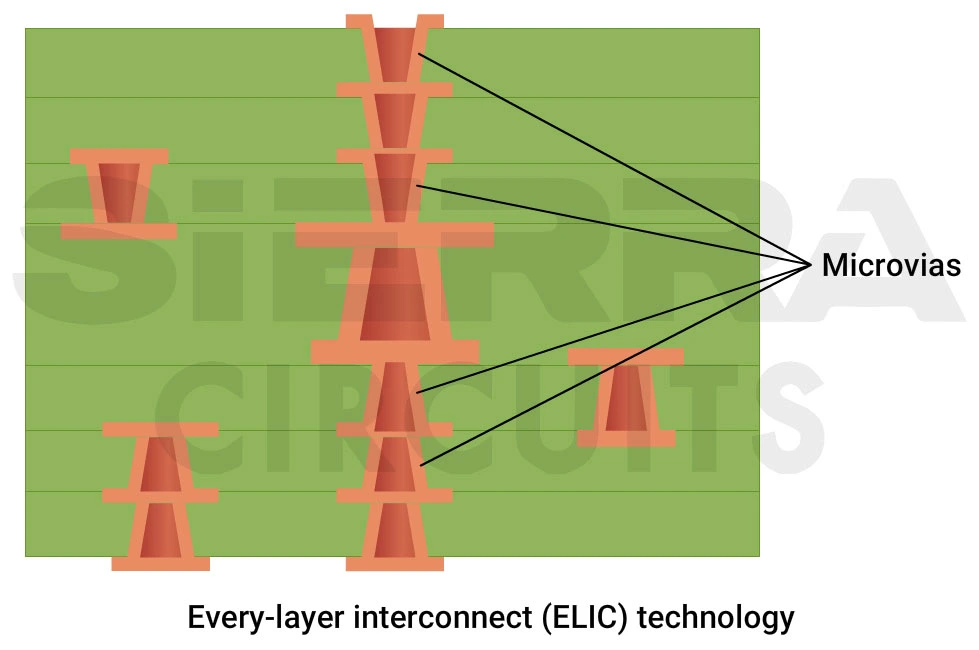
Key advantages of ELIC technology in humanoid robotics
- Stacked microvias, via-in-pad, and laser-drilled vias allow for dense and compact routing, which is essential for integrating high-speed processors and neural network accelerators used in AI-driven robotic modules.
- Unlike traditional PCBs, ELIC allows unlimited routing paths, enabling complex circuit layouts for high-performance AI modules, sensors, and actuators in humanoids.
- Laser-drilled microvias replace bulky through-hole vias, allowing direct layer-to-layer connections. This eliminates unnecessary internal structures, reducing PCB size and weight and improving wiring density.
- Sequential lamination is used to achieve a high layer count while preserving mechanical integrity, ensuring durability under continuous robotic operation.
- A new class of materials, known as build-up films, is specifically designed to support sequential lamination and laser-drilled via structures. These films utilize either a non-reinforced resin or a modified, ultra-thin reinforced layer, optimizing performance for advanced circuit designs. Their exceptionally low Dₖ values make them an excellent choice for high-speed, ultra-high-density applications.
Further, using low dielectric constant (Dₖ) and low dissipation factor (Df) materials, such as Isola I-Tera and I-Speed, ensures that high-speed signals maintain their integrity, reducing losses and optimizing high-speed data transmission for real-time robotic control.
Download our eBook to learn how to design efficient HDI PCBs.
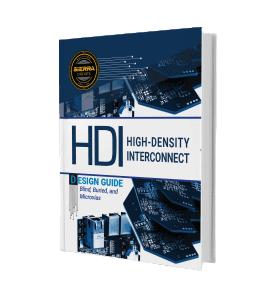
HDI PCB Design Guide
5 Chapters - 52 Pages - 60 Minute ReadWhat's Inside:
- Planning your stack-up and microvia structure
- Choosing the right materials
- Signal integrity and controlled impedance in HDI
- Manufacturing considerations for higher yields
Download Now
4. Embedded components and system-in-package (SiP)
Embedded component and SiP technologies enable the integration of AI chips, real-time control units, and power-efficient actuators within PCB layers, enhancing miniaturization and signal integrity.
Key advantages for humanoids:
- Capacitors and resistors are embedded within PCB layers, reducing external bulk and saving space.
- SiP technology integrates AI processors directly into the PCB, enabling faster real-time decision-making for motion control and environmental interaction.
- RF and power modules are embedded within PCB layers, minimizing signal loss and enhancing energy efficiency, critical for humanoid robots’ extended operation.
5. AI-driven PCB inspection and quality control
Given the complexity of humanoid robot PCBs, stringent quality control measures are essential to ensure error-free manufacturing. AI-driven inspection techniques play a pivotal role in detecting micro-defects that may not be visible to the human eye.
Key AI-based inspection techniques
- Automated optical inspection (AOI) systems are employed to analyze surface-level defects, ensuring that circuits are correctly fabricated. Machine learning models continuously improve defect detection, reducing false positives.
- High-resolution X-ray imaging is used to inspect ball grid array (BGA) connections and embedded components. AI algorithms detect hidden structural defects, such as solder bridges and voids.
- AI-driven predictive models assess printed boards’ durability by analyzing defect patterns. Machine learning forecasts potential failures, allowing proactive corrections before they impact performance, ensuring long-term durability for humanoid robotic systems.
IoT-enabled PCBs for smarter humanoids
The integration of IoT in PCB design is transforming smart robotics by enabling effective communication between robots and a wide range of sensors and devices. This enhanced connectivity allows robots to gather real-time environmental data, significantly improving their ability to operate autonomously.
For instance, IoT-enabled PCBs equip robots with advanced object recognition capabilities, reducing the need for human intervention and improving overall safety and efficiency, particularly in hazardous environments.
By embedding IoT within PCB design, humanoids become more adaptive and intelligent, with the ability to interpret and respond to their surroundings with greater accuracy. This increased level of interaction improves their precision and autonomy, making them more effective across various industries.
Key takeaways:
- The humanoid robot PCB market is rapidly expanding, driven by advancements in AI, automation, and miniaturized electronics.
- Flex and rigid-flex PCBs are widely used, enabling compact, lightweight, and adaptable designs.
- Power management boards regulate voltage, distribute energy efficiently, and include safety mechanisms for overload protection.
- Data exchange is facilitated through PCBs supporting CAN, UART, SPI, Wi-Fi, and Bluetooth for internal and external communication.
- Some humanoids use dedicated AI accelerators for deep learning-based vision, natural language processing, and reinforcement learning.
- Specialized PCBs regulate servo, BLDC, and stepper motors to ensure precise, smooth movement and coordinated articulation.
- Key manufacturing techniques include ultra-thin flexible substrates, polyimide-based materials, rolled annealed copper for ductility, and protective coverlay for enhanced endurance.
- Liquid crystal polymer (LCP)-based substrates support high-speed data transmission in AI, radar, and 5G applications.
- HDI PCBs for robotics with every-layer interconnect technology support ultra-compact, high-density PCBs for AI-driven robotic modules.
- IoT-enabled PCBs enhance real-time communication between robots and sensors for improved autonomy.
Designing PCBs for humanoid robots is a highly intricate process that demands careful attention to space, performance, durability, and environmental factors. By leveraging advanced materials and cutting-edge manufacturing techniques, engineers can create PCBs that seamlessly integrate into humanoid systems.
A well-optimized PCB not only enhances a robot’s agility and functionality but also extends its operational lifespan, enabling it to perform seamlessly in dynamic and demanding environments.
Connect with us to get your humanoid PCBs manufactured with precision.
Have questions on humanoid robotics PCB design? Post your queries on SierraConnect. Our PCB experts will answer them.
Start the discussion at sierraconnect.protoexpress.com